The High-Durability Mud Pump Wear Plate is an essential part of the fluid end system in drilling pumps. It is installed inside the cylinder, providing precise positioning and protecting the pump cylinder from wear. Crafted from high-quality forged 35CrMo alloy steel, our wear plates feature a nickel-plated surface with excellent wear resistance and corrosion protection.
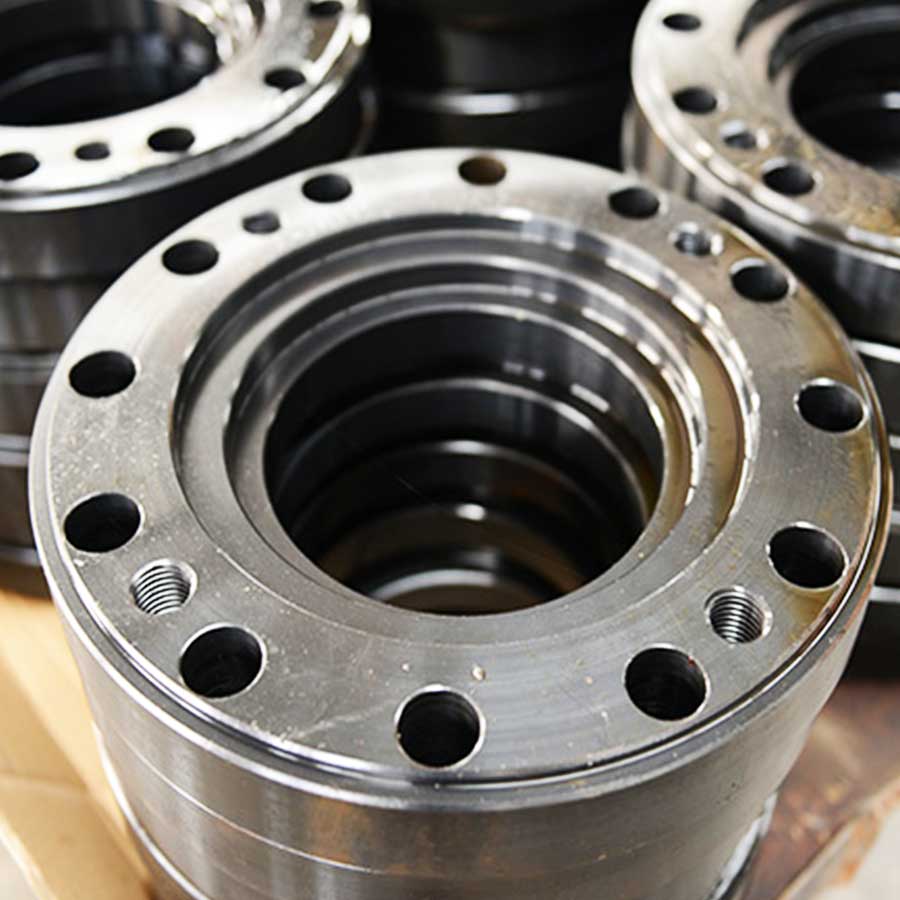
Our wear plates are designed to ensure optimal performance and longevity. The wear plate’s sealing surface, assisted by a spring-loaded mechanism, compensates for thermal expansion and contraction and minor wear from repeated valve cycles. This design prevents back pressure fluctuations from affecting the seal and keeps particulate matter from entering the sealing surface, ensuring consistent operation and reliability.
Features
- Self-Cleaning Seal Design: The valve seat’s open-structure seal surface design ensures that the valve disc stirs and removes the medium during each action, preventing internal material buildup commonly seen in other wear-resistant valves. The changing cycle of the flow path space induces a self-cleaning vortex effect, preventing material buildup, corrosion, and damage and maintaining good valve sealing.
- Zero Leakage: The unique self-cleaning seal surface and self-grinding design ensure an excellent valve closure effect, with leakage rates significantly lower than industry standards.
- Self-Grinding Design: During valve opening and closing, the disc remains in constant contact with the sealing surface. The medium acts as an abrasive, continuously repairing the damaged seal surface and maintaining good valve sealing.
- High Temperature and Corrosion Resistance: The valve disc and seat feature a metal-to-metal hard seal. The seal surface combines nickel-based and cobalt-based hard alloys, providing high hardness, corrosion resistance, oxidation resistance, and high-temperature resistance, suitable for various temperatures and harsh conditions.
- Linear and Angular Stroke Design: Different stroke modes can be adopted according to user requirements to meet various process needs.
Specifications Table
Parameter | Value |
---|---|
Material | Forged 35CrMo Alloy Steel |
Surface Treatment | Nickel Plating |
Application | Mud Pump Fluid End System |
Key Features | High Wear Resistance, Corrosion Resistance |
Function | Precise Cylinder Positioning, Protects Cylinder from Wear |
Self-Cleaning Design | Yes |
Leakage Rate | Significantly Lower than Industry Standards |
Seal Type | Metal-to-Metal Hard Seal |
Temperature Resistance | High |
Corrosion Resistance | High |
Stroke Design | Linear and Angular |
Role of Wear Plates in Pumps
Wear plates act as a protective barrier between the pump casing and the impeller. The impeller, a rotating component, generates pressure differences that move the fluid through the pump. As the impeller rotates, it causes friction against the pump casing, leading to wear and damage over time. Wear plates, typically made from durable materials like stainless steel or ceramics, provide a smooth surface for the impeller to slide against, reducing friction and evenly distributing the load on the pump casing, thereby extending the pump’s lifespan.