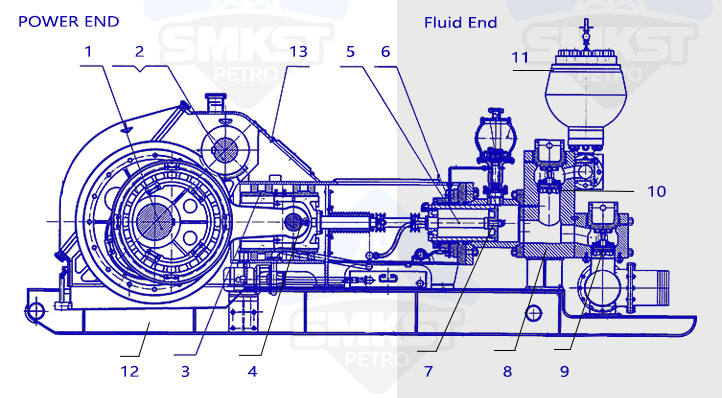
Published on: Nov 11, 2024
In oil and gas drilling, the mud pump serves as the core of the entire “circulatory system,” making it a critical piece of equipment for ensuring the smooth progress of drilling projects. By continuously circulating drilling fluid (mud) with specific viscosity and density into the wellbore, the pump provides cooling and lubrication for the drill bit, removes cuttings, and prevents well collapse. For those working in drilling, understanding the functionality and operation of mud pumps is essential.
In this article, an SMKST drilling engineer shares valuable insights into mud pumps, including their functions, structural design, operating principles, and best practices for use. This guide will help you understand how these pumps operate and their role in drilling.
Part 1: What Is Mud Pump?
A mud pump is a crucial equipment specifically designed for drilling operations. Often described as the “circulatory pump” of the drilling system or the “heart” of the mud circulation system, its primary purpose is to continuously and consistently inject mud into the wellbore. This process cools and lubricates the drill bit during high-speed drilling and removes cuttings from the wellbore, keeping it clean and stable.
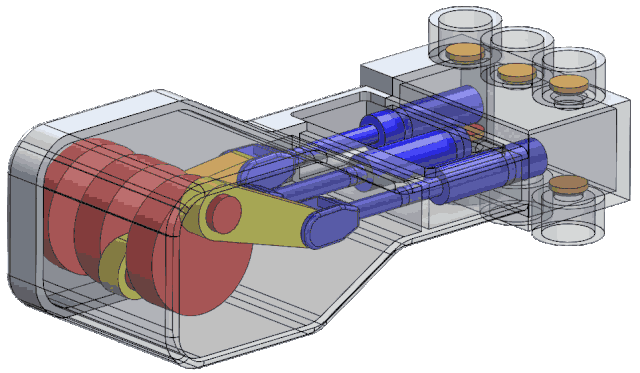
Mud pumps are indispensable in oil and gas drilling. By delivering high-pressure mud to the healthy bottom, they help maintain pressure balance in the wellbore, reducing the risk of wall collapse and ensuring safety and efficiency in drilling operations.
Part 2: Mud Pump Working Principle
Mud pumps can be divided into two main types: reciprocating and centrifugal. However, reciprocating plunger pumps, notably the F and 3NB series, are more commonly used in energy drilling projects. This section focuses on reciprocating mud pumps’ working principles and design features.
Read More: Drilling Mud Pump Types You Should Know >
Reciprocating mud pumps operate on a “pressure conversion process.” These pumps convert the motor’s rotational motion into the piston’s back-and-forth linear motion through a precise mechanical structure, transforming low-pressure mud into high-pressure mud.
This conversion involves two stages: the suction and discharge phases.
- Suction Phase: The piston moves backward, creating low pressure in the pump chamber, allowing mud to be drawn in.
- Discharge Phase: The piston moves forward, pushing the mud out at high pressure. This continuous cycle of suction and discharge ensures a steady, high-pressure mud flow during drilling.
Mud pumps consist of two main sections: the power end and the fluid end.
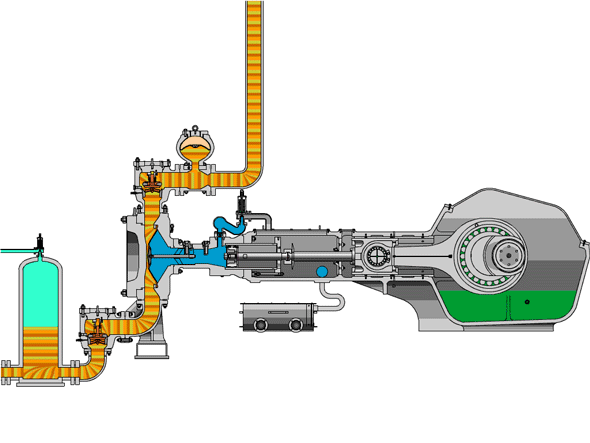
- Power End: Known as the “heart” of the mud pump, it converts the motor’s rotational movement into the piston’s reciprocating movement.
- Fluid End: This section converts the piston’s mechanical energy into the mud’s internal energy, compressing it to the high pressure needed for drilling. This “power conversion and transfer” design allows reciprocating mud pumps to function reliably under various drilling conditions.
Part 3: Structure and Components of Mud Pumps
Understanding the components of the power and fluid ends in a mud pump helps explain its operational principles. Below is an overview of the internal structure and key parts of an F-series mud pump commonly used in oil drilling.
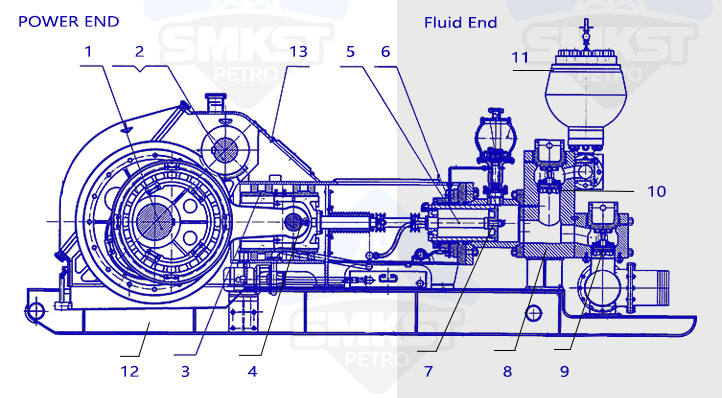
Power End Components:
- 1. Crankshaft: Drives the linear movement of the connecting rod and crosshead.
- 2. Drive Shaft: Transfers rotation to the crankshaft via gears.
- 3. Upper and Lower Guide Plates
- 4. Crosshead Assembly: Includes guide plates, crosshead, crosshead pin, pony rod, and other parts.
The power end transfers rotational movement from the drive shaft to the crankshaft via gears, which converts rotational force into a reciprocating motion. This motion then reaches the fluid end through the intermediate rod in the crosshead assembly.
Fluid End Components:
- 5. Piston Rod
- 6. Liner
- 7. Piston
- 8. Fluid Cylinder
- 9. Suction Valve
- 10. Discharge Valve
- 11. Air Chamber
The fluid end transmits the reciprocating force from the power end to the piston rod, causing the piston to move back and forth within the liquid cylinder. This movement generates the suction and discharge processes. The one-way suction and discharge valves deliver mud in a single direction through the pipeline.
Mud pumps have lubrication devices at critical points like chains, gears, bearings, and cylinder liners to ensure smooth operation. Additionally, a pulsation chamber is usually installed to absorb pump impact pressure, protecting high-pressure system components. For safety, mud pumps have pressure gauges and safety valves to monitor and protect the pump and the entire drilling system.
Part 4: Evaluating the Basic Performance of Mud Pumps
Knowing a mud pump’s key performance parameters is crucial, whether for rig assembly, design, operation, maintenance, or replacement. These parameters directly impact the pump’s efficiency and suitability for specific tasks. Below are the essential performance indicators for mud pumps:
Performance Indicator | Definition and Description |
Theoretical Displacement (Q) | The volume of fluid discharged by the pump per unit of time reflects the pump’s output under ideal conditions and determines the appropriate pump size. |
Working Pressure (p) | The force exerted per unit area at the pump’s discharge outlet. Higher working pressure helps counteract downhole pressure, stabilizing the wellbore. |
Rated Power and Efficiency (N) | Rated power is the input energy per unit time to the pump’s drive shaft. Effective power (Nr) indicates the energy added to the fluid by the pump. Efficiency, as the ratio of effective power to input power, reveals energy utilization. |
Stroke Rate (n) | The number of piston strokes per unit time. Higher stroke rates increase mud discharge but may raise wear, so adjustments should align with operational conditions. |
Stroke Length (S) | The distance the piston travels in each stroke, determining the volume of mud drawn in and discharged each time. Stroke length is a vital parameter for adjusting pump output in the design phase. |
Conclusion
Mud pumps are the core equipment in drilling operations. Their working principles, structural design, and performance indicators are crucial for safe and efficient drilling. Understanding the function and operation of mud pumps enables operators to manage equipment effectively, ensuring bottom-hole cooling and wellbore pressure balance, which boosts productivity. In future drilling projects, the scientific use and maintenance of mud pumps will continue to play a pivotal role in improving safety and efficiency.
For inquiries on purchasing F-series, 3NB series, or other drilling mud pumps and accessories from China, please contact SMKST Petro.