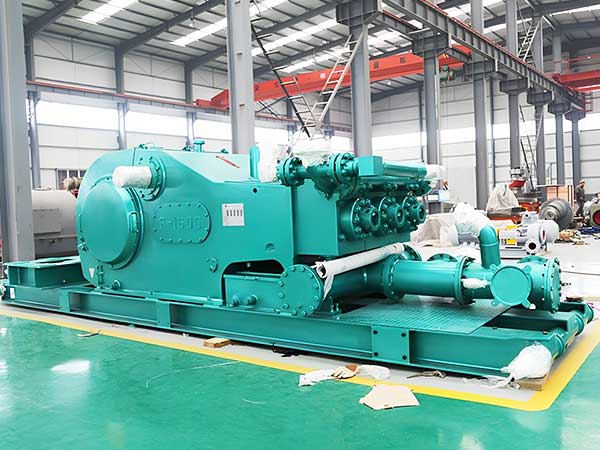
Published on: July 14, 2024
Mud pumps are essential in oil, gas, and geothermal drilling, playing a critical role in ensuring smooth and safe drilling operations. Their primary functions include circulating drilling fluid, cooling the drill bit, and removing cuttings, which maintain the stability of the wellbore and prevent blockages.
Read More: How Does a Mud Pump Work?
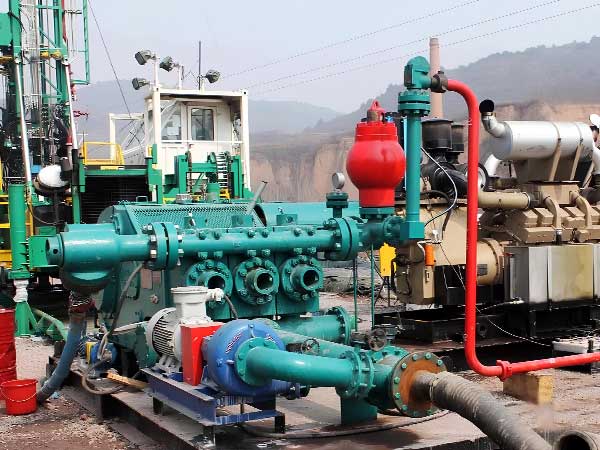
By circulating drilling fluid, mud pumps effectively dissipate the heat generated during drilling, preventing the drill bit from overheating and getting damaged. The circulation also helps clear the cuttings from the bottom of the well, preventing blockage and ensuring wellbore stability. Additionally, mud pumps help maintain wellbore pressure, preventing incidents such as blowouts.
This article classifies mud pumps used in oil drilling rigs from five perspectives: structure type, stroke type, application, flow rate and pressure, and drive method. This classification will help you understand the characteristics and application scenarios of different types of mud pumps, enabling you to make informed choices.
Part 1: Classification by Structure Type
The cylinder is a vital component of the mud pump. Each cylinder contains a piston that moves back and forth to intake and discharge drilling mud. The number of cylinders determines the structure of the mud pump, directly affecting its flow rate and pressure capability. Generally, more cylinders mean a higher flow rate and more stable pressure output but also higher costs. Below are three common structural types, their features, and application scenarios.
1) Three-Cylinder Mud Pump
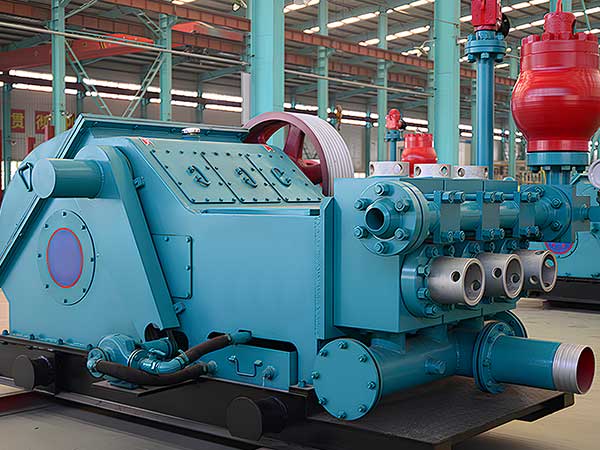
Three-cylinder mud pumps are the most common type, featuring three cylinders and pistons. They provide higher flow and pressure, making them suitable for most drilling operations. These pumps are popular due to their good performance-to-cost ratio and relatively low maintenance costs.
- Representative Models: F series (e.g., F-500, F-1000)
- Suitable Rig Type: Medium rigs, widely used in land drilling operations and medium-depth drilling.
2) Five-Cylinder Mud Pump
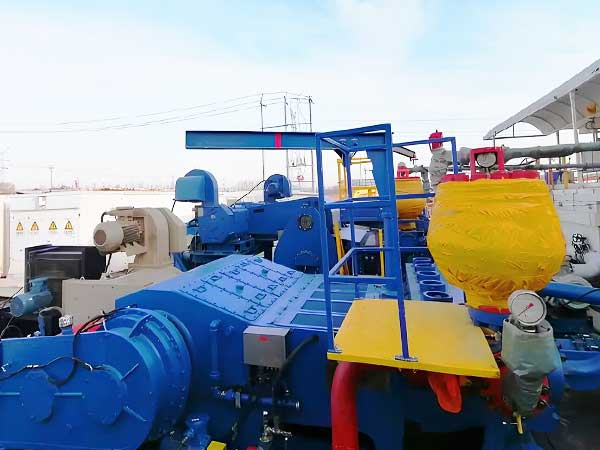
Five-cylinder mud pumps offer even higher flow and pressure, suitable for demanding and complex drilling operations. Due to their more complex structure and higher performance, they are typically used in deep wells and high-pressure environments.
3) Double-Cylinder Mud Pump
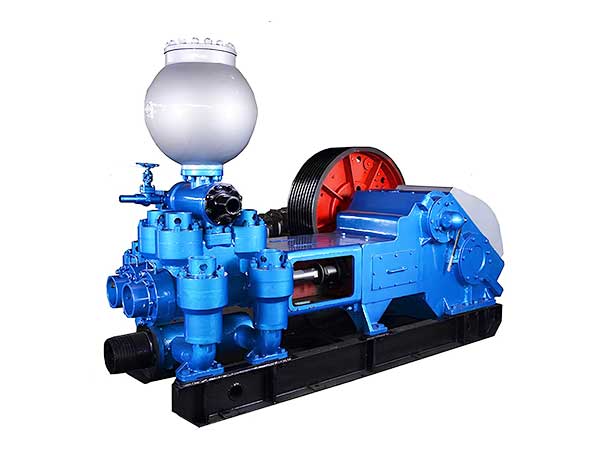
Double-cylinder mud pumps have two cylinders and double-acting pistons. They are designed to be simple, easy to maintain and operate, and are suitable for supplying flushing fluid in geological exploration, geothermal drilling, water well drilling, shallow oil, and coal seam drilling operations.
- Representative Model: BW1200/7
Part 2: Classification by Stroke Type
The stroke type of a mud pump mainly affects its flow rate, pressure stability, and operational efficiency. Based on stroke type, mud pumps can be divided into single-acting and double-acting pumps. Choosing the appropriate stroke type can better meet the needs of different drilling operations.
1) Single-Acting Mud Pump
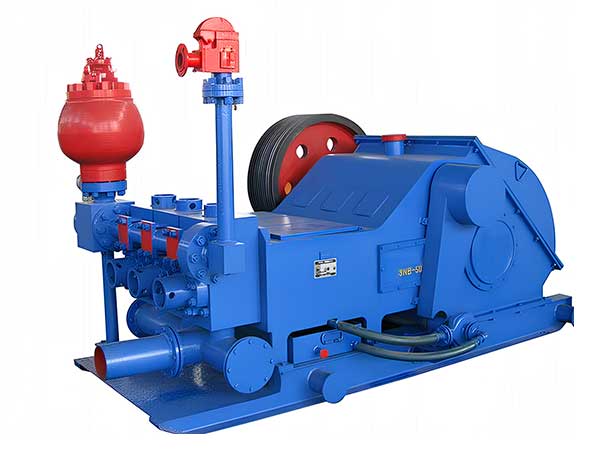
Single-acting mud pumps perform one intake and one discharge operation per stroke. Due to their simple structure, they are generally more reliable and easier to maintain, making them a commonly used type in the drilling industry. However, they typically offer lower flow and efficiency compared to double-acting pumps.
- Representative Models: F series (e.g., F-800), 3NB series (e.g., 3NB-1300)
2) Double-Acting Mud Pump
Double-acting mud pumps perform two intakes and two discharges per stroke, resulting in higher flow compared to single-acting pumps. Despite their more complex structure, they excel in operations requiring high flow rates and are suitable for larger-scale drilling projects.
- Representative Models: Gardner Denver FX series, National 12-P-160
Part 3: Classification by Flow Rate and Pressure
The flow rate and pressure of a mud pump are key indicators of its performance. As drilling depth increases, the requirements for flow rate and pressure also rise. Shallow operations require lower flow and pressure, which is suitable for low-flow, low-pressure pumps. Conversely, deeper operations necessitate high-flow, high-pressure pumps.
1) Low-Flow, Low-Pressure Mud Pump
Low-flow, low-pressure pumps are suitable for shallow wells and low-pressure environments, typically used in small-scale and straightforward drilling projects. These pumps have a simpler structure, lower cost, and are easier to operate and maintain.
- Representative Models: 3NB-500
- Suitable Rig Type: Small rigs, shallow drilling, and well servicing operations, simpler drilling projects.
2) High-Flow, High-Pressure Mud Pump
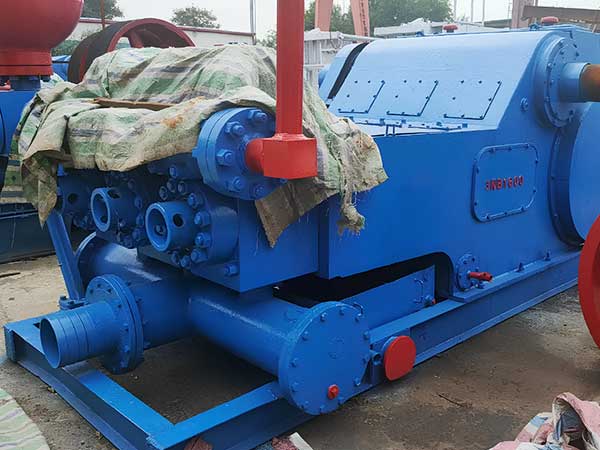
High-flow, high-pressure pumps handle larger volumes of mud and provide high output pressure, which is suitable for deep wells and high-pressure environments. Due to their complex design and high-performance requirements, these pumps are generally more expensive but excel in complex and demanding drilling operations.
- Representative Models: F-1600, F-2200
- Suitable Rig Type: Large rigs, deep drilling, and high-pressure operations, complex drilling projects.
Part 4: Classification by Application
Mud pumps can be classified based on their application environment and usage scenarios into land drilling pumps and offshore drilling pumps. Each type has specific design features to suit the respective drilling environment and conditions.
1) Land Drilling Mud Pump
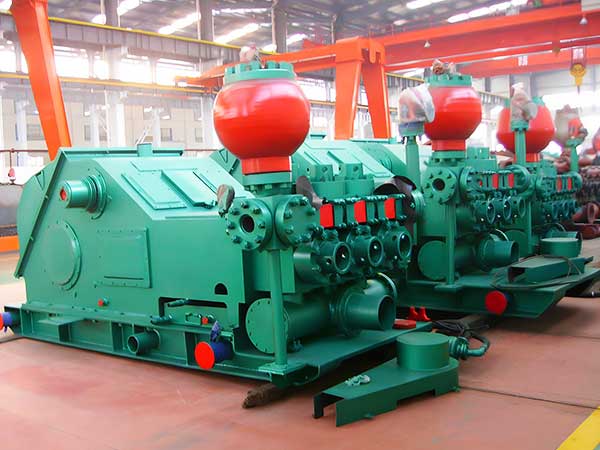
Land drilling pumps are designed for onshore environments. They are typically lighter for easier transport and installation. They are suitable for various onshore drilling projects, including shallow and medium-depth drilling operations. Due to less harsh environmental conditions, these pumps do not require the high corrosion resistance and durability of offshore pumps.
- Common Models: F-500, F-800, 3NB-500, 3NB-1300
2) Offshore Drilling Mud Pump
Offshore drilling pumps are designed for marine environments. They are suitable for offshore drilling projects, including nearshore and deep-sea operations, and have higher corrosion resistance and durability to withstand seawater and harsh weather conditions. These pumps also have higher material standards and stronger protective capabilities.
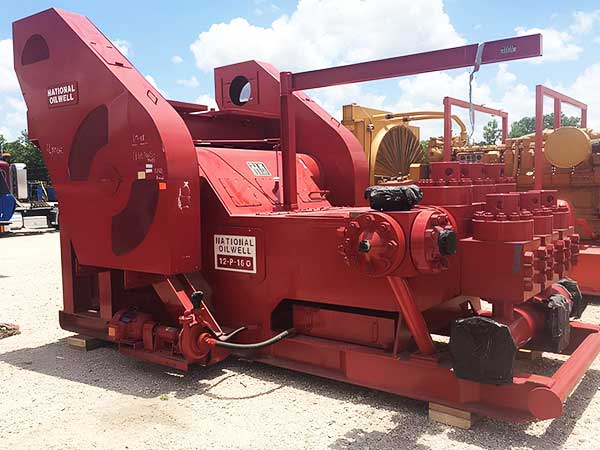
- Common Models: F-1600, 3NB-1600
Part 5: Classification by Drive Method
Mud pumps can be categorized by their drive and transmission methods into mechanical drive pumps and hydraulic drive pumps. Each drive method has its advantages and application scenarios to meet different drilling operation needs.
1) Mechanical Drive Mud Pump
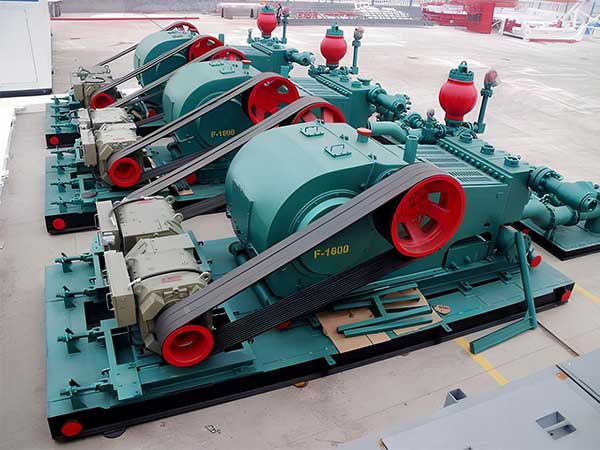
Mechanical drive pumps rely on engines or electric motors to transmit power through mechanical devices like belts, gears, or chains to the pump components. These pumps have a simple design, are easy to maintain, and are suitable for most drilling environments. The skid-mounted F-1600 model mud pump shown above utilizes an electric motor as the power source and employs belt transmission to drive the mud pump.
- Common Models: F series, 3NB series
- Procurement Advice: Suitable for various land drilling projects, ideal for environments requiring high reliability and easy maintenance.
2) Hydraulic Drive Mud Pump
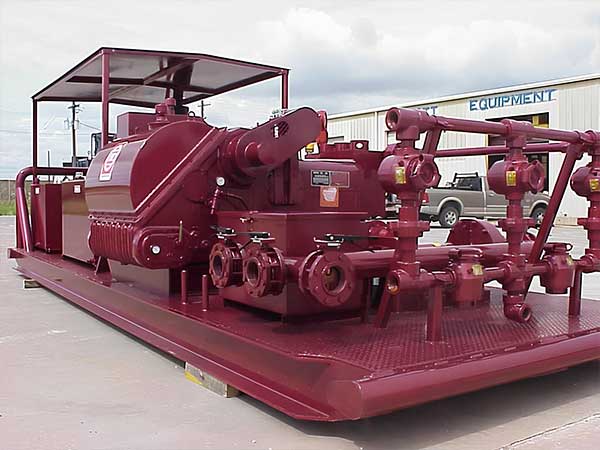
Unlike mechanical drive pumps, hydraulic drive pumps use a hydraulic system to transfer power to the pump components despite being initially powered by electricity or diesel engines. These pumps offer precise control and high efficiency, making them suitable for drilling operations requiring high precision and variable speed.
- Common Models: National Oilwell Varco series, Gardner Denver series
- Procurement Advice: This product is suitable for complex and demanding drilling projects, such as offshore and deep drilling operations. It is ideal for environments requiring precise control and high efficiency, but consider the hydraulic system’s maintenance and operational demands.
How to Choose the Right Mud Pump Type for Drilling Rig?
Selecting the right mud pump for oil drilling requires considering multiple factors, including operational environment, drilling depth, flow and pressure requirements, drive method, and cost. For land drilling projects, especially medium-depth and high-load operations, the F series and 3NB series mechanical drive mud pumps (e.g., F-1000 or 3NB-1300) are ideal due to their high reliability, easy maintenance, and lower cost. These models typically use gear transmission, providing sufficient flow and pressure to meet complex drilling needs while offering maintenance and operational cost advantages.
Example Configurations:
- 3000 HP Land Rig: Equip with 3-4 F-2200 mud pumps
- 2000 HP Land Rig: Equip with 3 F-1600 mud pumps
- 1500 HP Land Rig: Equip with 2 F-1600 mud pumps
- 1000 HP Land Rig: Equip with 2 F-1300 mud pumps
- 750 HP Land Rig: Equip with 2 F-1000 mud pumps
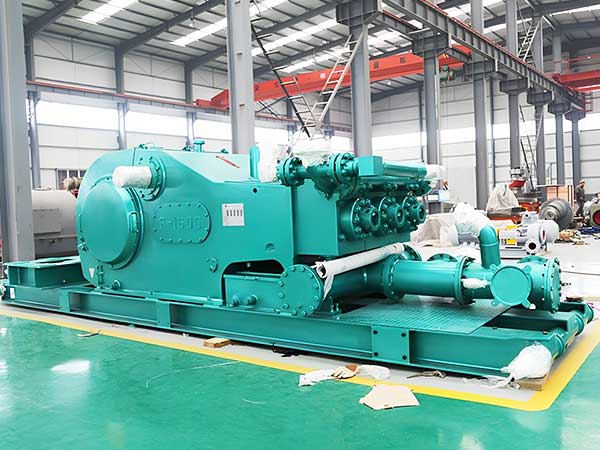
Given the unique environmental conditions and high corrosion, hydraulic drive mud pumps (e.g., National Oilwell Varco 12-P-160) are recommended for offshore drilling projects. These models offer high corrosion resistance and precise control, suitable for complex operations requiring high precision and variable speed. Although the initial cost of hydraulic systems is higher, their efficiency and long lifespan can reduce overall operational costs over time.
Conclusion
Choosing the right mud pump is crucial as it is core equipment in oil drilling operations. Understanding the classifications based on structure type, stroke type, application, flow rate and pressure, and drive method helps match your drilling project’s specific needs. When selecting, consider differences in quality and cost among similar models from different suppliers. For high-cost-performance mud pumps from China, feel free to consult us.