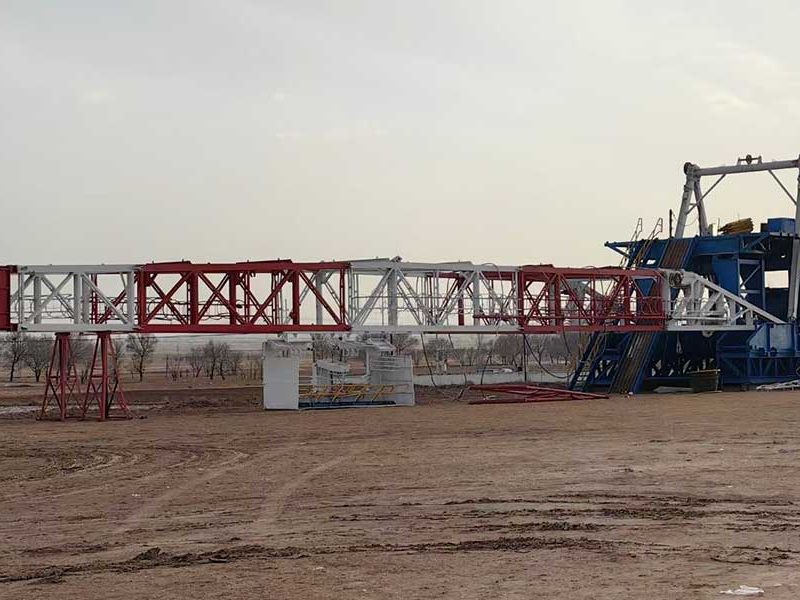
Published on: Jun 15, 2024
Land rigs are powerful tools for drilling oil wells and are crucial in natural gas, geothermal energy, and other fields. As global energy demand continues to rise, the market size for land rigs used in energy extraction increases yearly. According to the latest report by Mordor Intelligence on Land Rig Market Size, the market size of land rigs is expected to reach $43.62 billion by 2024 and grow to $51.70 billion over the next five years, with a compound annual growth rate of 3.46%.
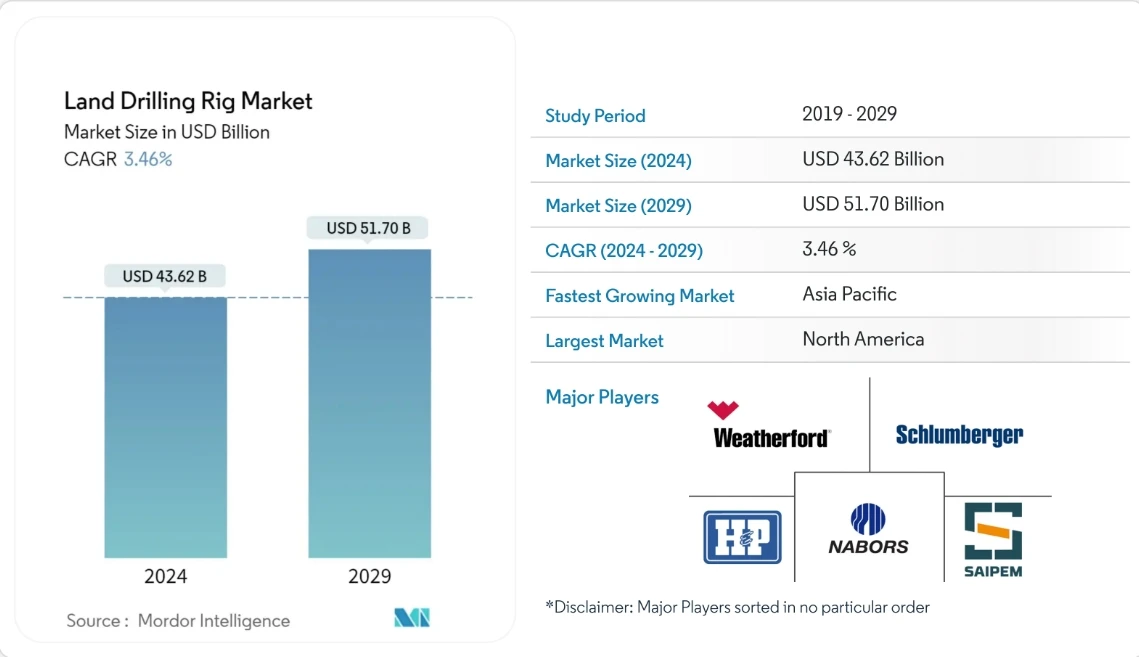
Purchasing the right land rig is crucial for energy companies and service providers. Different land rigs vary significantly in cost, drilling depth, operational efficiency, and ease of installation and disassembly. As a professional company specializing in the sale and service of land rigs, SMKST aims to help you understand the current classifications of land rigs and the unique features and applications of each type through this article so you can make an informed investment in your drilling project.
What Is Land Rig?
Broadly speaking, land rigs, which are key tools for exploring and extracting underground resources, can be classified into four major categories: oil and gas rigs, geothermal rigs, water well rigs, and core drilling rigs. However, these classifications are not absolute.
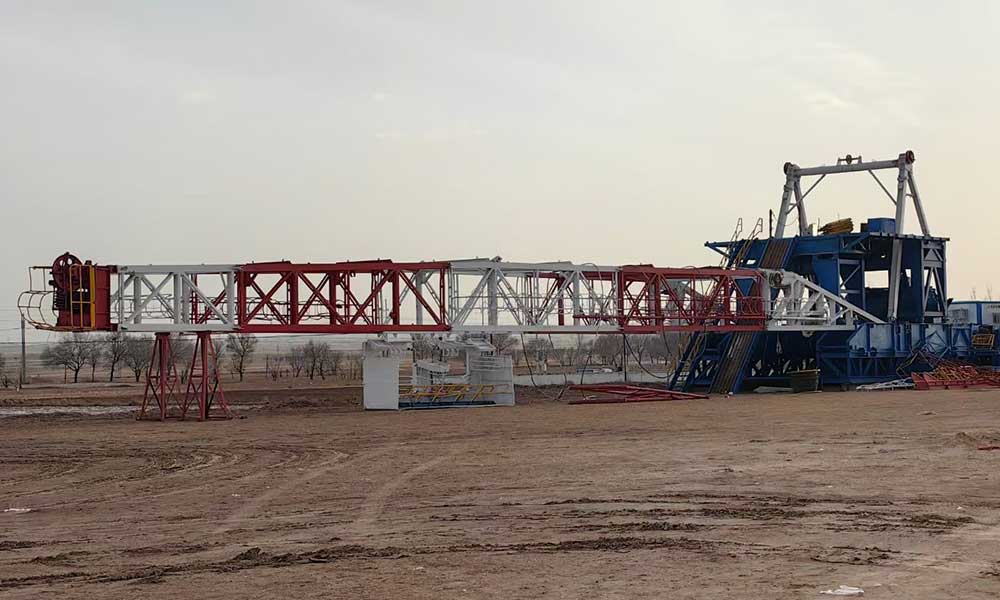
For example, a core drilling rig can be used for water well construction at certain depths, and geothermal rigs can be used for shallow oil exploration. In most cases, land rigs are considered oil and gas rigs. Next, we will focus on land rigs that can be used for oil, natural gas, and geothermal energy drilling.
All Types of Land Oil Rigs
Land oil rigs can be classified from different perspectives. Here, we will discuss the classification based on drilling methods, drive equipment and methods, main transmission types, and drilling depth, covering 20 types of rigs in total.
1. By Mobility
Based on mobility, land rigs can be categorized into 4 types: skid-mounted rigs, fast-moving rigs, trailer-mounted rigs, and truck-mounted rigs. Each type offers unique advantages suited to different drilling scenarios and terrains.
Let’s explore these four types of rigs in detail.
(1) Skid-mounted Rigs
As the name suggests, skid-mounted rigs are built on skids that allow for limited movement. These rigs balance mobility and stability, making them popular for many drilling operations. The concept of skid-mounted rigs dates back to the early days of oil exploration, evolving from completely stationary rigs to ones that provide some degree of repositioning capability.
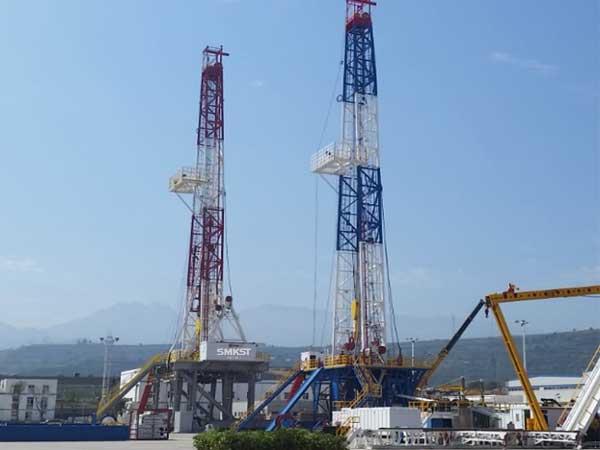
A distinctive feature of skid-mounted rigs is that the rig and its components are divided into modular units for skid-mounting. This design facilitates rapid hoisting and transportation, enabling quick assembly and disassembly. Such modularization allows for efficient setup and relocation, which is particularly advantageous in dynamic drilling environments.
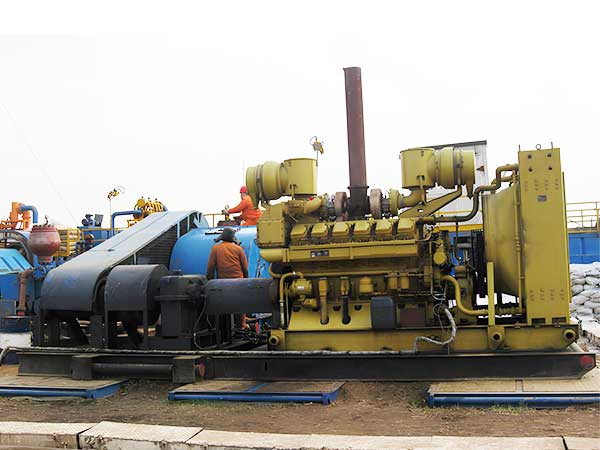
Skid-mounted rigs are the most prevalent type of drilling rig. They are suitable for deeper drilling depths and adaptable to most geographical environments. Their ability to move short distances without complete disassembly is especially useful in fields where multiple wells are drilled from a single pad. However, for longer distances, these rigs typically require heavy-duty equipment like bulldozers or winches for relocation, which can be time-consuming and labor-intensive.
(2) Fast-moving Rigs
Fast-moving rigs represent a significant leap in rig mobility. Designed to address the increasing demand for rapid relocation between drill sites, these rigs can be quickly dismantled, transported, and reassembled. This efficiency is crucial in modern drilling operations, especially in areas where multiple wells are drilled across a wide area.
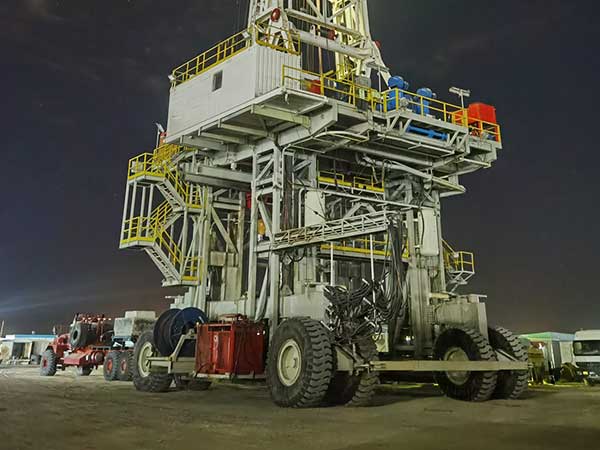
The key to their speed lies in their modular design and advanced hydraulic systems. Many components are pre-assembled and can be easily connected or disconnected. This design reduces rig-up and rig-down times and minimizes the need for large crews during moves. Fast-moving rigs have become increasingly popular in unconventional oil and gas developments, where the ability to move between closely spaced wells quickly is paramount.
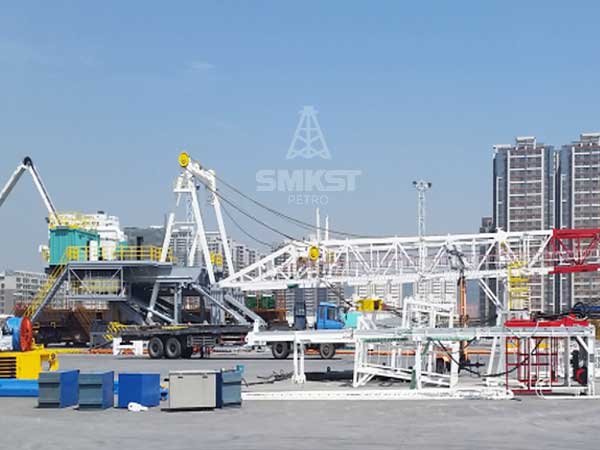
(3) Trailer-mounted Rigs
A trailer-mounted drilling rig is a mobile drilling unit installed on a trailer or semi-trailer. It’s widely used in fields like oil, natural gas, geothermal energy, and water well drilling. The most notable feature of this rig is its high mobility; the entire setup can be transported by trailer, making it easy to move quickly between different drilling sites. Thanks to its compact design, the trailer-mounted drilling rig is suitable for operations in confined spaces and can work efficiently in various complex terrains and environments.
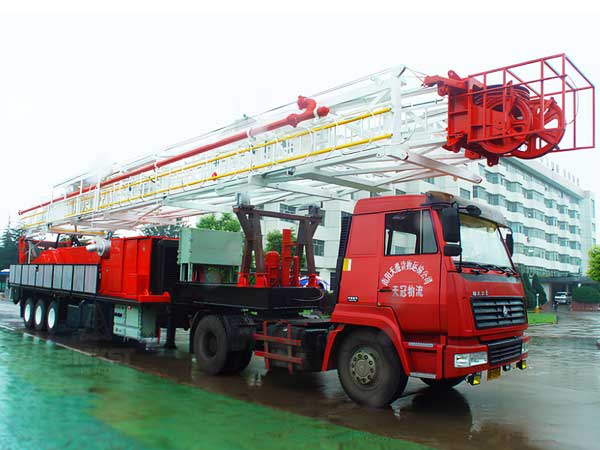
This rig type is mainly used for medium to shallow-depth drilling, typically ranging from a few hundred to five thousand meters deep. Compared to large fixed rigs, trailer-mounted rigs have relatively lower investment and operational costs and can be deployed and dismantled more quickly. This makes them ideal for small exploration projects or initial exploratory work.
(4) Truck-mounted Rigs
Truck-mounted rigs represent the pinnacle of long-distance mobility in land drilling operations. These rigs are fully mounted on truck chassis, allowing for rapid deployment and relocation over significant distances. The concept of truck-mounted rigs emerged from the need for highly mobile drilling units, especially in exploratory drilling and workover operations.
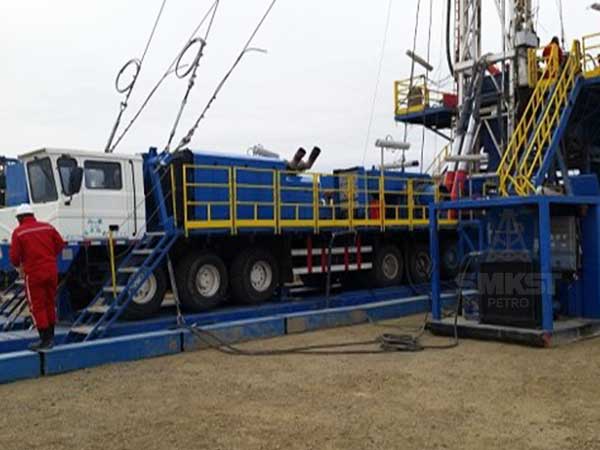
The primary advantage of truck-mounted rigs is their ability to move between widely separated locations using regular roads quickly. This makes them ideal for exploratory drilling, where wells may be scattered across a large geographical area. Additionally, their compact design often allows for easier permitting and reduced site preparation, making them suitable for environmentally sensitive areas or locations with limited access.
2. By Drilling Method
Based on the drilling method, there are four types of rigs: percussion drilling rigs, rotary table drilling rigs, downhole motor rigs, and top drive system rigs. Let’s examine these four types of rigs in detail.
(1) Percussion Drilling Rigs
Percussion drilling, also known as cable tool drilling, originated in the Northern Song Dynasty of China and was initially used for salt well extraction. Although rarely used today, its low cost and small footprint made it valuable in early resource exploration.
The first well, which was over a thousand meters deep in human history, was drilled using this method. The main drawbacks are its slow drilling speed and high operational costs. Despite being phased out with modern advancements, percussion drilling has left an indelible mark on the history of drilling technology and laid the foundation for future developments.
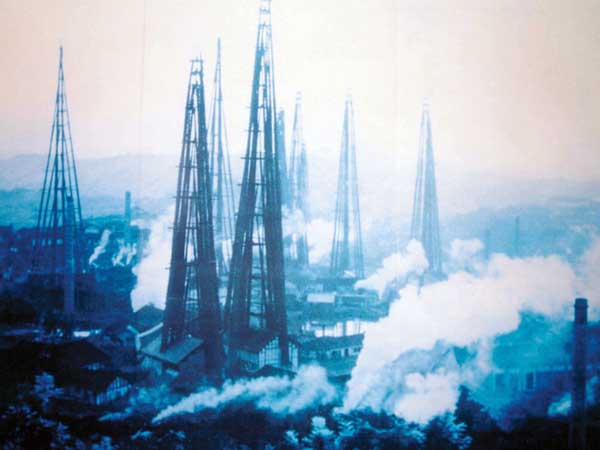
(2) Rotary Table Drilling Rigs
Rotary table drilling rigs, which match the rotary drilling method, are the most common equipment in land drilling today. They drive the drill pipe through a rotating table, transferring torque to the drill bit to break the rock. Drilling fluid circulates through the hollow drill string, continuously clearing the cuttings to allow deeper penetration. Compared to percussion drilling, rotary table drilling rigs have a faster drilling speed.
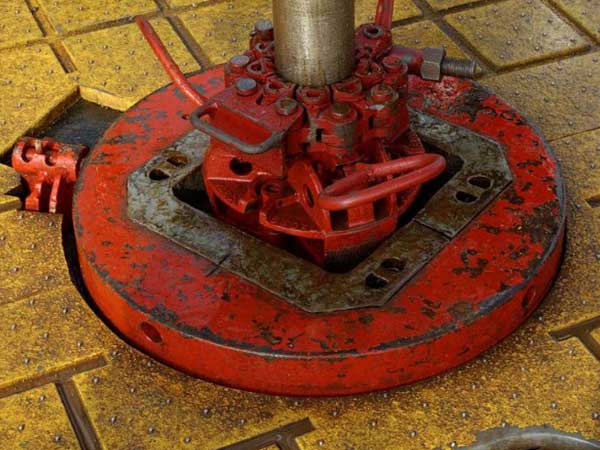
However, they face two major challenges: first, during normal drilling, only single drill pipes can be connected, resulting in low efficiency and high labor intensity. Second, during tripping operations, the risk of pipe sticking is high, and the inability to rotate the drill string or establish mud circulation often leads to missed opportunities to handle incidents, causing severe drilling accidents.
(3) Downhole Motor Rigs
In the drilling rig family, downhole motor rigs are highly advanced, primarily driven by fluid or electricity. Imagine fluid-driven screw motors (such as Dyna-Drills, Navi-Drills, or Turbodrills) rotating underground—it’s like a high-speed dance beneath the surface.
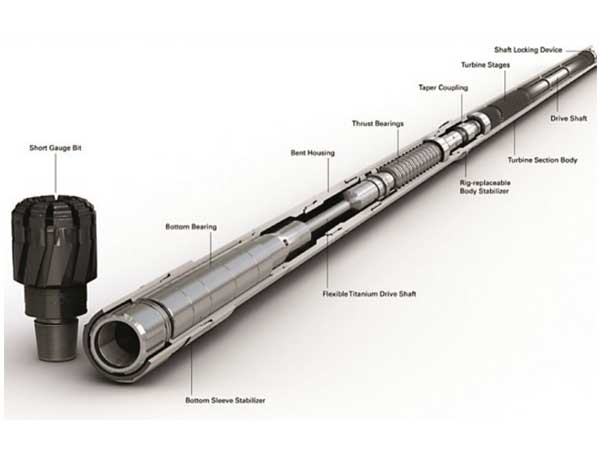
These rigs offer several advantages, including higher mechanical penetration rates, improved drill string operating conditions, reduced drilling tool failures, and extended service life. Additionally, they can use lightweight drill pipes with low power consumption, making them ideal for technically demanding drilling operations such as directional wells, multi-lateral wells, and re-entry drilling.
(4) Top Drive System Rigs
If downhole motor rigs are the high-speed dancers, then top drive system rigs are the heavyweights. Designed to address the challenges faced by traditional rotary table rigs, the top drive system moves the power section from the rig’s base to the top, directly driving the drill string, thereby making drilling operations more efficient.
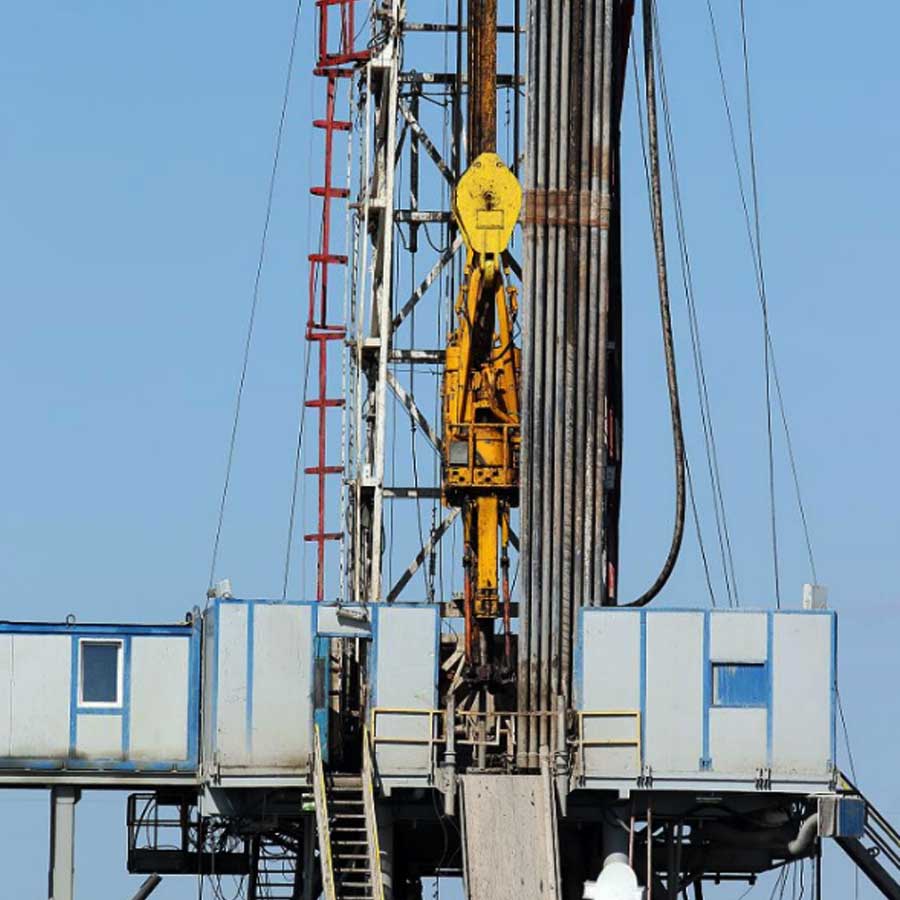
Its high efficiency allows quick recovery from pipe sticking and re-establishment of mud circulation, significantly reducing the risk of drilling accidents. Furthermore, it has two internal blowout preventers (IBOPs) to respond to any signs of well influx quickly, ensuring operational safety. The top drive system has become a standard in the oil drilling industry, and its numerous advantages will be explored further in our future blog posts.
3. By Type of Drive Equipment
Land rigs can also be classified based on the type of drive equipment, including diesel, electric, and grid-powered rigs. Let’s explore the characteristics of each type:
(1) Diesel-Driven Rigs
As the name suggests, diesel-driven rigs rely on the power of diesel engines, which drive the rig through mechanical or hydraulic transmission methods. The primary advantage of these rigs is their self-sufficiency—they can operate anywhere as long as the fuel tank is full. They have stable rotation speeds and strong mobility, making them ideal for field operations in remote locations. However, they do have some drawbacks, such as lower transmission efficiency and higher operating costs compared to electric rigs, and they can be quite noisy.
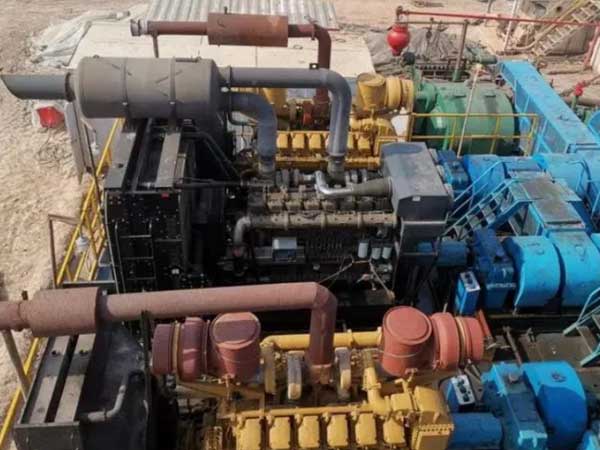
(2) Electric-Driven Rigs
Rigs using DC or AC motors fall under the category of electric-driven rigs. These rigs can be directly driven by electric motors or through transmission devices to drive the working units. Their advantages include high transmission efficiency, lower operating costs, simpler maintenance, and suitability for long-term continuous operations.
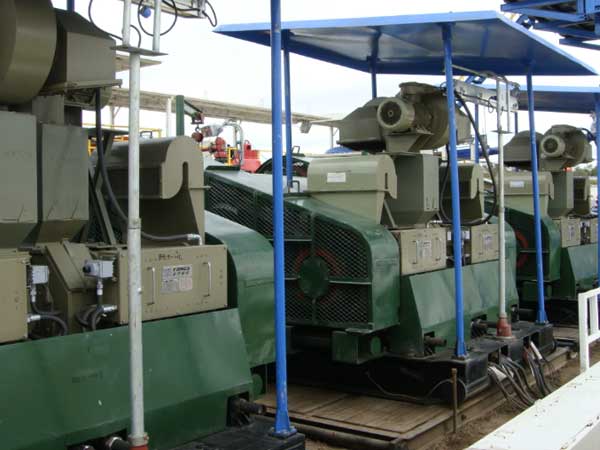
(3) Grid-Powered Rigs
Technically a subset of electric-driven rigs, grid-powered rigs rely on industrial power grids for electricity, directly using high-voltage grid power, eliminating the need for diesel generator sets. In the context of energy conservation and emission reduction, grid-powered rigs are gradually becoming market favorites, especially in China. They offer high economic efficiency and meet modern green environmental requirements, making drilling operations both efficient and eco-friendly.
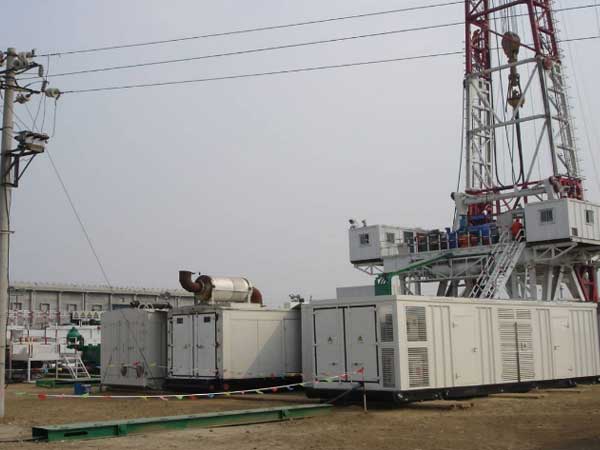
4. By Drive Method
Land rigs can also be classified based on their drive methods into three main types: unified drive rigs, individual drive rigs, and grouped drive rigs. Each has unique characteristics and suitable use cases:
(1) Unified Drive Rigs
Imagine a team where all members follow the commands of a single leader—this is the principle behind unified drive rigs. The drawworks, mud pumps, and rotary table are driven by 2-4 power units connected together. The main advantage of this configuration is efficient power utilization. If one part encounters a problem, other parts can compensate for continuous operation. However, its complexity cannot be underestimated; installation and adjustments can be challenging for technicians, and the transmission efficiency is relatively low.
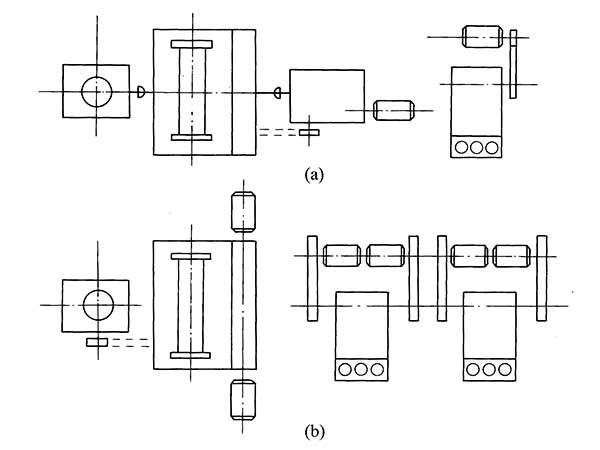
(2) Individual Drive Rigs
In this setup, each work unit has its own generator, akin to each band member bringing their own instrument. This method of transmission is straightforward and convenient to install. However, like a band struggling to stay perfectly in sync, individual drive rigs typically have lower power utilization efficiency and can appear bulkier overall.
(3) Grouped Drive Rigs
Grouped drive rigs balance the two previous methods, where the three main work units are divided into two groups for driving. This setup is neither as complex as a unified drive nor as inefficient as an individual drive, offering a compromise. It allows for flexibility in installing work units at different heights or dispersed locations, enhancing operational flexibility and site adaptability. For example, for rigs with derrick heights of 7 to 9 meters, the main draw works can be installed without the hassle of placing it on a high platform.
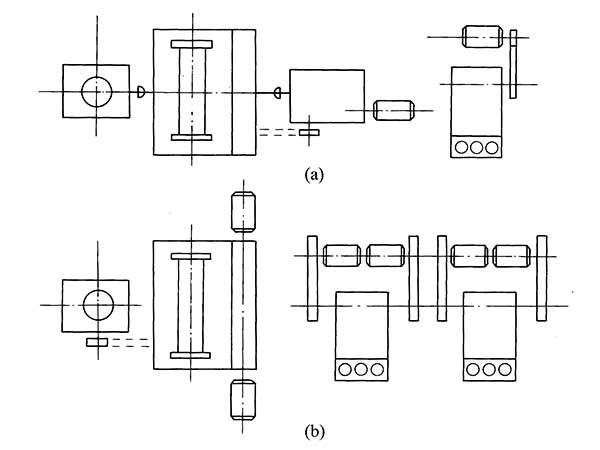
5. By Main Transmission Type
In land rigs, the main transmission type is a crucial criterion for classification. Here, we introduce five types of transmission methods.
(1) Belt Drive Rigs
These rigs use E-type or V-shaped belts as the core transmission device, unifying the power of multiple diesel engines to drive various work units and auxiliary equipment. Imagine a massive rubber band connecting multiple strong athletes, working together to push through a tough task. The widely used V-belt drive rigs have the advantage of a smooth transmission process and are relatively simple and convenient to manufacture and maintain, much like handling a regular belt.
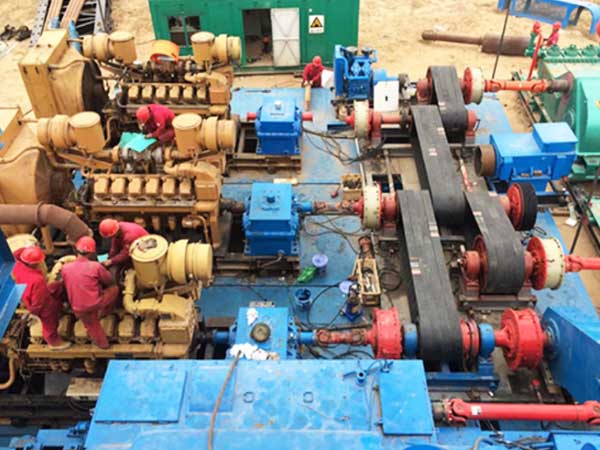
(2) Chain Drive Rigs
In these rigs, the main transmission relies on chains. Imagine a series of chains connecting and driving 2-4 diesel engines, providing robust power with a wide range of speed variations. However, ordinary chains cannot meet such high-intensity demands, requiring specially designed petroleum-specific chains to ensure smooth operation. While the power of these rigs is impressive, they demand exceptionally strict chain quality, necessitating specially designed chains to handle extreme conditions.
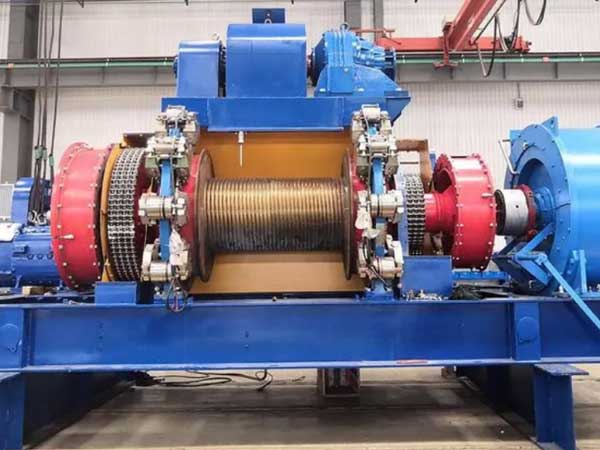
(3) Gear Drive Rigs
Think of a precise gear system that provides high transmission efficiency and maintains a compact structure. Gear drive rigs use gears and universal shafts to drive the drawworks and rotary table, allowing for faster operation and a smaller footprint. Although gear drive has many advantages, such as easy maintenance and good interchangeability, it also has drawbacks—high-power spiral gears are difficult to manufacture, and on-site repair or replacement can be challenging if problems arise.
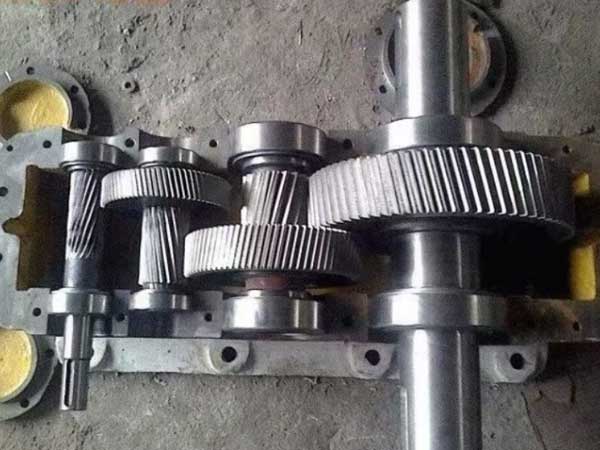
(4) Hydraulic Drive Rigs
If gear-drive rigs are precision mechanical masters, then hydraulic-drive rigs are the artists of fluid power. These rigs use hydraulic transmissions, offering smooth and flexible power transmission that adapts well to external load changes. They can achieve step-less speed variation and reverse braking, optimizing the rig’s operational performance and making complex drilling operations smoother.
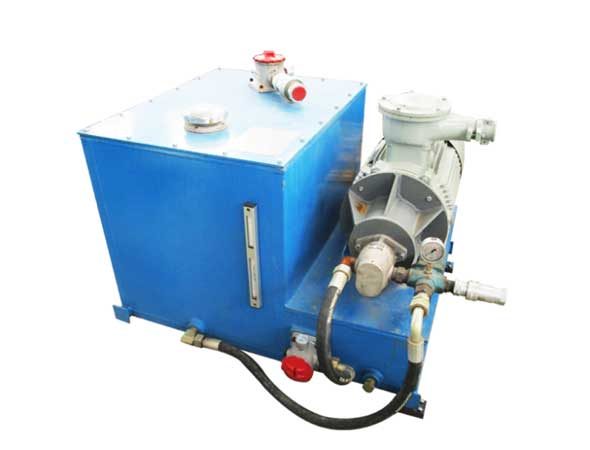
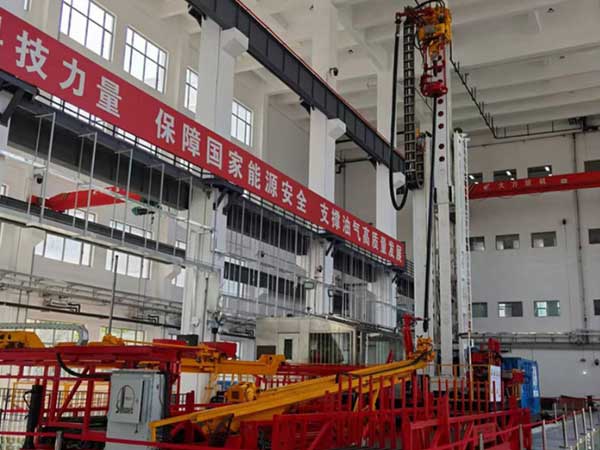
(5) Electric Drive Rigs
Electric drive rigs are becoming increasingly popular in modern drilling technology due to their simple structure and high transmission efficiency. These rigs rely entirely on electricity to transmit kinetic energy, making installation and mobility easy and convenient. They also facilitate the automation and intelligent control of drilling operations. Electric drive rigs are undoubtedly an ideal choice for drilling projects that prioritize high efficiency and environmental friendliness.
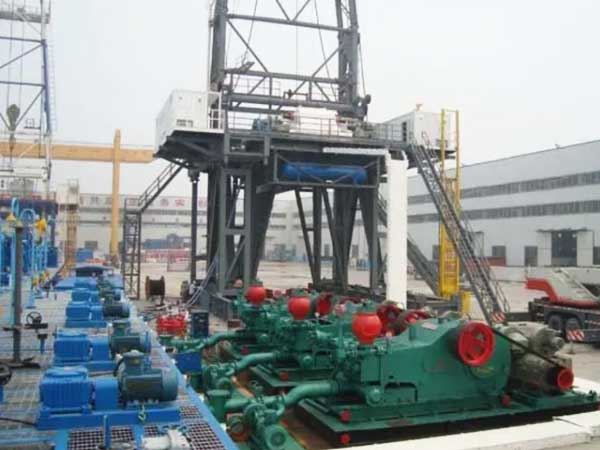
6. By Drilling Depth
(1) Shallow Well Rigs
Designed for exploring relatively shallow energy sources, these rigs typically drill to no more than 1,500 meters. Shallow well rigs are primarily used for geological surveys, core sampling, water well drilling, and seismic and shot hole drilling. They are ideal tools for operations in shallower strata. Combined with mobile rigs, they can provide faster and more flexible energy exploration.
(2) Medium-Depth Well Rigs
When drilling needs to reach depths of 1,500 to 3,000 meters, medium-depth well rigs come into play. These rigs are designed for deeper exploration and can reach areas that shallow well rigs cannot access.
(3) Deep Well Rigs
Deep well rigs, which drill to depths of 3,000 to 5,000 meters, are crucial for exploring deeper geological structures. These rigs can access most resource-rich strata, making them indispensable oil and gas extraction tools.
(4) Ultra-Deep Well Rigs
Ultra-deep well rigs are the true explorers of great depths, drilling to 5,000 to 9,000 meters. They are designed to reach deeper into the Earth and can handle the most extreme drilling depths.
(5) Extra-Deep Well Rigs
These rigs are the giants of the drilling industry, drilling to depths exceeding 9,000 meters. China’s independently developed 12,000-meter automated rig not only breaks the 10,000-meter depth barrier but also signifies that China’s deep earth oil and gas drilling capabilities and supporting technologies have reached internationally advanced levels. This achievement makes China the second country globally and the first in Asia to drill beyond 10,000 meters on land.
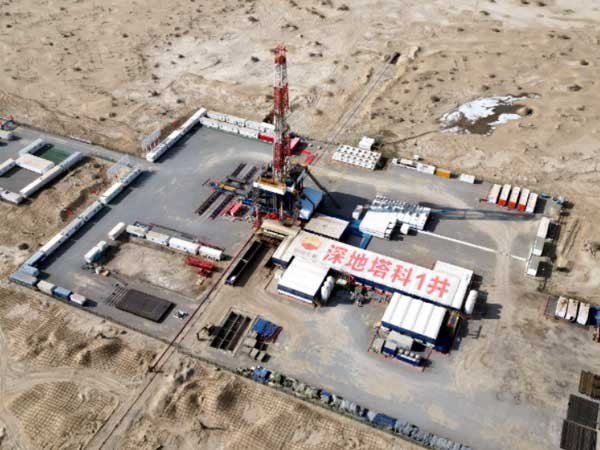
Conclusion
This article provides an in-depth explanation of the various classifications of land oil rigs, from drive methods to different drilling depth requirements. We explored rigs’ characteristics, advantages, and drawbacks under each category. These classifications reveal the flexibility and specialization of land oil rigs in adapting to various challenging operations. Each type of rig offers precise and efficient solutions for oil extraction.
As global energy demand grows, SMKST is committed to providing efficient and reliable drilling solutions, offering top-tier land oil rigs and unparalleled customer service. Our advanced product designs optimize operational efficiency and cost-effectiveness even in the harshest environments, ensuring our clients achieve the best oil and gas drilling results. Choosing SMKST means partnering with a leader in cutting-edge oil extraction technology.