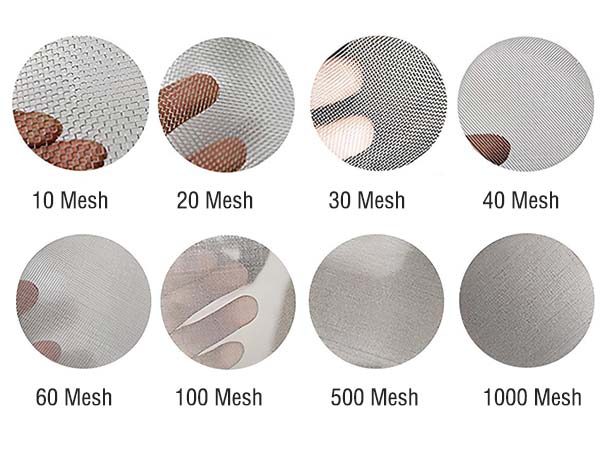
Published on: Mar 21, 2025
In oil and gas drilling operations, the shale shaker acts as the first line of defense in solids control. Its performance directly impacts how clean the drilling fluid stays. One of the most critical factors behind that performance? Choosing the right shaker screen size. But “size” doesn’t just mean the screen’s length and width. It also includes mesh count, API designation, and D100 cut point. These technical specs affect how well the screen separates solids from fluid.
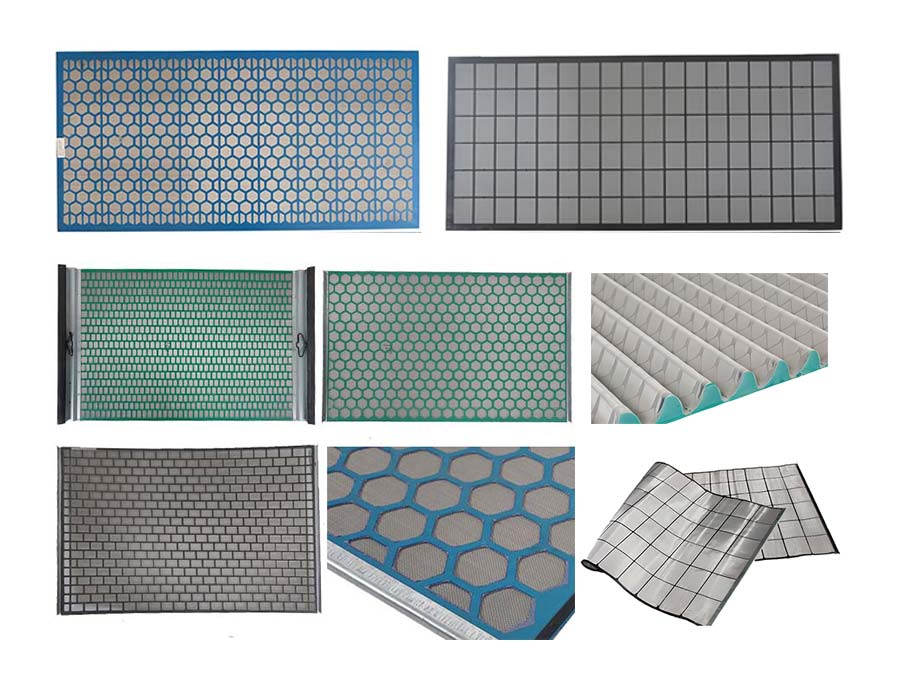
To select the ideal screen for your oil or gas drilling rig, you’ll need to factor in well conditions, mud properties, cutting size, and the shaker’s design. Properly matching screens to each drilling phase results in better separation, lower costs, and smoother operations overall.
The Three “Sizes” of Shale Shaker Screens
When you first hear about shaker screens, your instinct might be to ask, “How fine is the mesh?” or “What’s the size?” But if you only focus on one number, you might end up choosing the wrong screen for the job. To pick the right one, you need to look at three key dimensions: Mesh count, API designation, and Physical dimensions.
1. Mesh Count
If you’ve worked with shakers before, “mesh count” is probably the first thing that comes to mind. When someone says an “80 mesh” screen, they’re talking about a screen woven with 80 wires per inch. The higher the mesh number, the smaller the openings—and the finer the particles it can filter. But there’s a trade-off: finer mesh can slow down the flow rate and reduce fluid handling capacity.
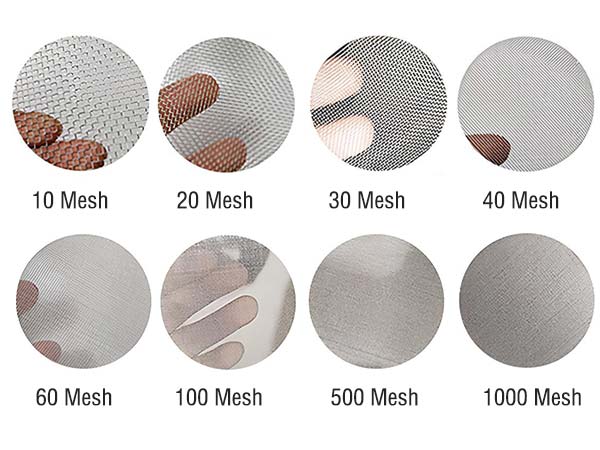
Conversely, screens with lower mesh counts let more mud through and offer faster flow, but they miss finer solids. It’s a balancing act.
Another thing to remember: not all “80 mesh” screens are made the same. Wire thickness and weave pattern vary between manufacturers. So even if two screens have the same mesh number, their actual separation performance might differ. That’s why the oilfield has widely adopted the API Screen Number system—to create a more reliable standard.
Unlike mesh count, the API number reflects actual tested performance, especially the D100 cut point—the particle size at which the screen removes 100% of solids in lab testing. If you only rely on mesh count, your screen might not perform as expected. But when you use the API rating, you get a better idea of the screen’s real-world performance.
2. API Screen Number
You’ve probably seen tags that read “API 100” or “API 120.” These aren’t just marketing terms—they follow the API RP 13C standard. Each API number represents a range of particle sizes the screen is capable of removing, based on lab testing.

For example, an API 100 screen captures solids between 137.5 to 165 microns. If you’re drilling in fine formations and need to trap smaller cuttings, you might go with an API 140 or API 200 screen.
Even if two screens are labeled “80 mesh” or “120 mesh,” as long as they share the same API rating, you can count on similar cut-point performance in the field.
Here’s a quick reference chart of common API designations and their D100 ranges:
API Number | D100 Range (μm) |
API 20 | 780.0 – 925.0 |
API 25 | 655.0 – 780.0 |
API 30 | 550.0 – 655.0 |
API 35 | 462.5 – 550.0 |
API 40 | 390.0 – 462.5 |
API 45 | 327.5 – 390.0 |
API 50 | 275.0 – 327.5 |
API 60 | 231.0 – 275.0 |
API 70 | 196.0 – 231.0 |
API 80 | 165.0 – 196.0 |
API 100 | 137.5 – 165.0 |
API 120 | 116.5 – 137.5 |
API 140 | 98.0 – 116.5 |
API 170 | 82.5 – 98.0 |
API 200 | 69.0 – 82.5 |
API 230 | 58.0 – 69.0 |
API 270 | 49.0 – 58.0 |
API 325 | 41.5 – 49.0 |
API 400 | 35.0 – 41.5 |
Note: API numbers are not direct conversions from mesh count. They’re based on test data. So while two “Mesh 80” screens may perform differently, two “API 80” screens should give similar cut-point results—regardless of who made them.
3. Dimension (Physical Screen Size)
Beyond API rating, the physical dimensions of the shaker screen are just as critical. If you’ve worked with different shaker brands, you know the screens aren’t one-size-fits-all. You might come across sizes like 585×1165 mm for a Mongoose screen or 695×1050 mm for a Derrick FLC500.

These dimensions determine whether the screen fits properly on a specific shaker model. They also affect the screen’s frame tensioning method and whether it’s flat or wave-shaped. Even the best-rated screen won’t work if it doesn’t physically fit.
That’s why, before buying or replacing screens, always double-check the shaker model. Better yet, provide the exact length, width, and thickness to your supplier to avoid any compatibility issues.
Here’s a quick look at some popular shaker models and their screen dimensions:
Shaker Brand / Model | Typical Screen Size (mm) | Notes |
MI-Swaco Mongoose | 585 × 1165 | Composite frame ~11.5 kg; Steel frame ~13.5 kg |
Derrick FLC500 | 695 × 1050 | Available in flat (PWP) or pyramid (PMD) design |
NOV Brandt Cobra | 635 × 1250 | Both composite and steel frames available |
VSM300 (Scalping Deck) | 685 × 940 | Different decks use different sizes (Primary / Secondary) |
Tricks:
- Mesh tells you how fine the screen is woven.
- API rating reflects actual separation performance.
- Dimension ensures the screen fits your equipment.
How to Choose the Right Shaker Screen Size
When selecting shaker screens for a drilling project, finer isn’t always better, and one-size-fits-all doesn’t work either.
1. Your Well Conditions Dictate Screen Fineness
Start with the well. Deeper wells often produce finer cuttings and demand higher fluid clarity. In those cases, you’ll likely need finer screens, like API 140 or API 200, to capture small solids. But for shallow sections—especially when drilling through soft formations with large cuttings—you’ll want coarser screens like API 60 or API 80. These allow more fluid to pass through and handle higher flow rates, even if they’re less precise.
Mud properties also matter. High-density, high-viscosity muds tend to clog finer mesh quickly. That slows down processing and cuts efficiency. On the other hand, if your drilling fluid is thin, clean, and flows well, you can go for finer mesh to improve solids control. As the well goes deeper, your screens usually need to get finer. One screen type won’t work from top to bottom.
2. Not All Screens Fit Every Shaker
Even if you’ve picked the right API number, it’s not enough. You need to confirm whether the screen physically fits your shaker. For example, the MI-Swaco Mongoose shaker uses screens sized 585 × 1165 mm, while the Derrick FLC500 needs 695 × 1050 mm screens. If the size is off—even by a bit—the screen won’t fit or seal properly. That means lost time and money.
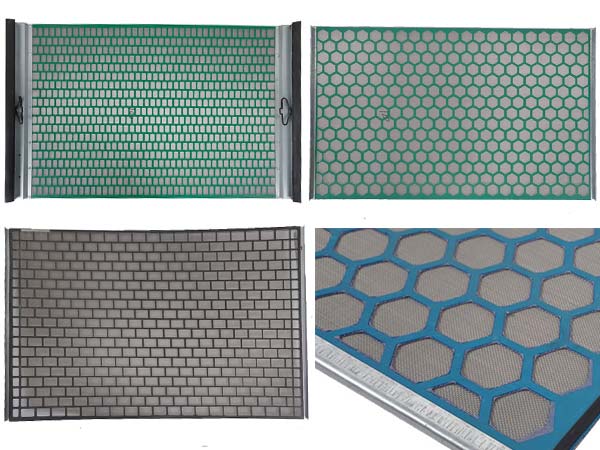
Also, different brands use different mounting systems. Some screens have hook strips, while others use composite frames with locking tabs. If you’re unsure, it’s best to tell your supplier exactly which shaker model you’re using. Better yet, send them a sample screen or a detailed size drawing. It’ll save a lot of back-and-forth.
3. API vs. Mesh vs. D100: Do You Know the Difference?
As mentioned earlier, the API screen number is now the most reliable industry standard for gauging screen performance. But if you tell your supplier, “I need a 100 mesh screen,” don’t be surprised if they ask: “Do you mean Mesh 100 or API 100?” Because they’re not the same.
Here’s a simple example:
An API 120 screen has a D100 cut point between 116.5 to 137.5 microns. That means it can reliably remove medium-fine solids—perfect for mid-to-late stages of drilling when cuttings get smaller.
If you’re unfamiliar with API ratings, you can work backward from the D100 cut size. This tells you what particle size you want to capture, which is especially helpful when drilling through tough zones like shale or clay-rich formations.
4. Finer Mesh Isn’t Always Better—or Pricier
A common myth on site is that finer mesh means better quality. This is not true. In high-viscosity or high-solids sections, a fine screen—like API 200—might clog fast, tear easily, and need frequent replacement. That’s wasteful, not efficient.
At the same time, going too coarse to save money can cost you more. If you use a loose mesh on high-value drilling mud, it’ll let fine cuttings pass through. That means your desanders and centrifuges have to work harder—and those are expensive systems to run.
5. The Smart Move? Think in Stages
The best approach is to treat shaker screens as part of a flexible strategy. When solids are heavy, start with coarser screens like API 60–80 and switch to finer ones like API 140 or 200 as the well deepens and formations tighten. This way, you reduce downtime, extend screen life, and maintain high separation efficiency without blowing your solids control budget.
Global Shale Shaker Screen Sizes by Brand
Each shaker series has strict requirements for screen length, width, edge design, and mounting style. A screen might have the right mesh and material, but if the size doesn’t fit—it simply won’t work.
To make sourcing easier, we’ve put together a comparison chart listing screen sizes for the world’s leading shaker brands. Whether you’re running MI-Swaco, Derrick, NOV Brandt, Elgin, FSI, or Vortex, you’ll find the corresponding screen specs right here. This saves time and helps avoid mismatches.
(And yes—SMKST offers high-quality replacement screens that match all the specs below. More affordable, made in China. Click here to contact our team.)
1. MI-Swaco Series
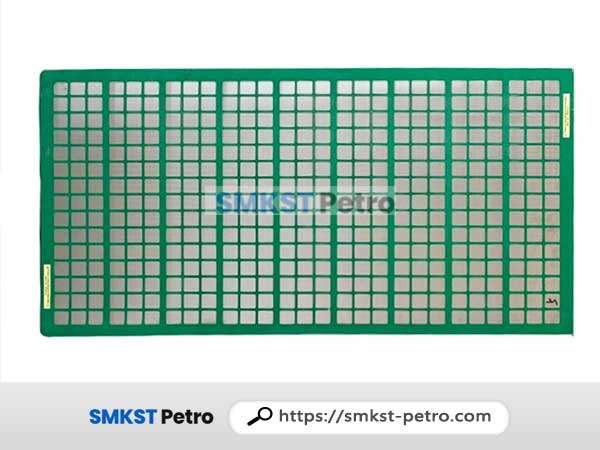
MI-Swaco is one of the most widely used brands on-site. Its composite frame offers a larger effective screen area, lighter weight, and corrosion resistance—ideal for tough drilling conditions.
Model | Dimensions (mm) | Frame Type | Compatible Equipment | Weight (kg) |
Mongoose | 585 × 1165 | Composite / Steel Frame | Mongoose Shaker / Cleaner | Composite ~11.5 kg
Steel ~13.5 kg |
MD Series | 622 × 655 | Composite Frame | MD-2 / MD-3 Shale Shaker | ~7 kg |
ALS Series | 1143 × 1213 | Hook Strip (Flat) | ALS 4×4 Shale Shaker | ~7 kg |
2. Derrick Series
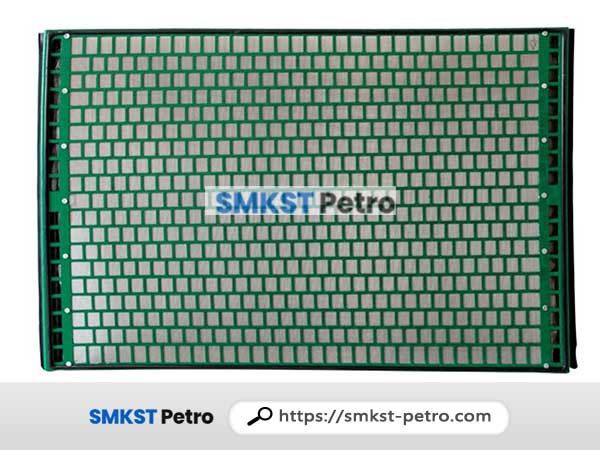
Derrick’s pyramid screens increase effective area through a three-dimensional design—ideal for high-precision applications.
Model | Dimensions (mm) | Screen Type | Compatible Equipment |
FLC500 Series | 695 × 1050 | Flat (PWP) / Pyramid (PMD) | Flow Line Cleaner 500 (3 or 4-panel) |
FLC2000 Series | 697 × 1053 | Flat (PWP) / Pyramid (PMD) | Flow Line Cleaner 2000 (3 or 4-panel) |
Hyperpool | 570 × 1070 | Pyramid (PMD) | Hyperpool Series Shakers / Cleaners |
Dual Pool 600 | 710 × 626 | Pyramid (PMD) | Dual Pool Series Shakers / Cleaners |
3. NOV Brandt Series
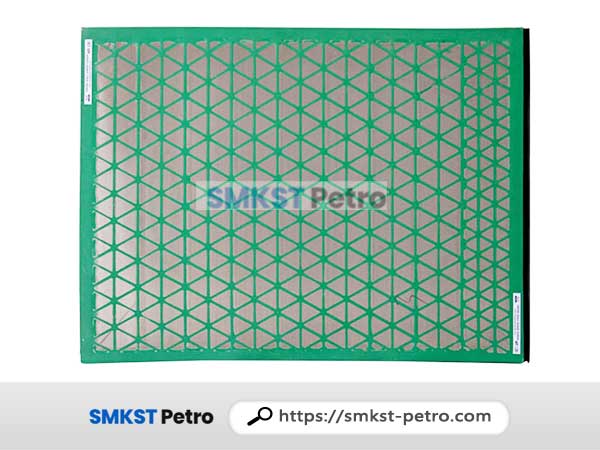
The VSM300 features a unique 3-deck layout (scalping / primary / fine), requiring different screen sizes for each layer.
Model | Dimensions (mm) | Frame Type | Compatible Equipment |
Cobra / Venom | 635 × 1250 | Composite / Steel Frame | Cobra, King Cobra, Mini Cobra, Venom, LCM-2D, LCM-3D |
VSM300 (Scalping) | 685 × 940 | Composite / Metal Frame | VSM300 Shaker – Scalping Deck |
VSM300 (Primary) | 685 × 890 | Composite / Metal Frame | VSM300 Shaker – Primary Deck |
VSM300 (Secondary) | 685 × 203 | Composite / Metal Frame | VSM300 Shaker – Secondary (Fine Screening) Deck |
4. FSI (Fluids Systems) Series
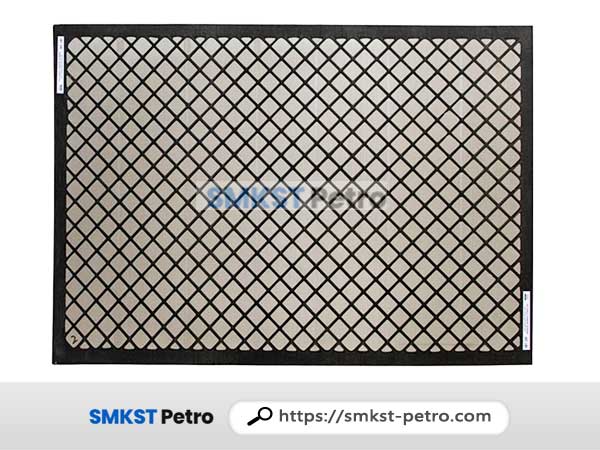
A practical and economical option, often used on land rigs. Also suitable for high-performance desanding systems.
Model | Dimensions (mm) | Frame Type | Compatible Equipment |
Fluids System 29×42 | 737 × 1067 | Composite Frame | FSI Shakers / Cleaner Series |
5. Vortex Series
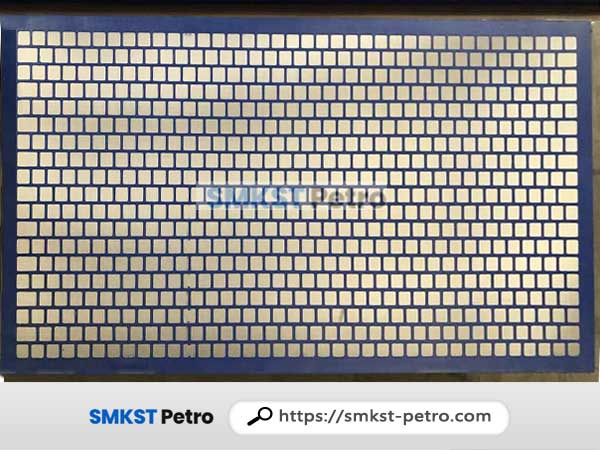
Known for its steel frame design, this screen suits cost-sensitive jobs. Composite versions are available on request.
Model | Dimensions (mm) | Frame Type | Compatible Equipment |
Vortex Screen | 610 × 1175 | Steel Frame | Vortex Shaker Series |
6. Elgin / Kemtron Series
Popular in North America and the Middle East. Built tough and designed for quick change-outs.
Model | Dimensions (mm) | Frame Type | Compatible Equipment |
KPT 28 | 715 × 1250 | Steel / Composite Frame | Elgin / Kemtron KPT 28 Series |
🔍 Quick Tip: How to Choose a Screen Fast?
You can just tell us the following information:
- Shaker brand and model (e.g., Derrick FLC500, Swaco Mongoose)
- Desired API rating or cut point (e.g., API 120, D100 = 116–137.5 μm)
Not sure about screen size or model?
No problem—just send us a photo of the screen or a used sample, and we’ll match the right replacement for you fast.
Final Thoughts
When we talk about “shale shaker screen size,” it’s not just about mesh count or physical dimensions. It’s a multi-factor decision—combining shaker type, screen design, API standards, and real-world good conditions.
By understanding how screens work, choosing them, installing and maintaining them, and staying up-to-date with the latest trends, you can boost your solids control efficiency, extend screen life, and cut overall drilling costs.
From a practical standpoint, we always recommend that technical teams and procurement work closely with screen suppliers or equipment manufacturers. Share key info like the API number, expected cut point, and mud properties. That way, you get the best-fit screen configuration—faster, smarter, and more cost-effective.