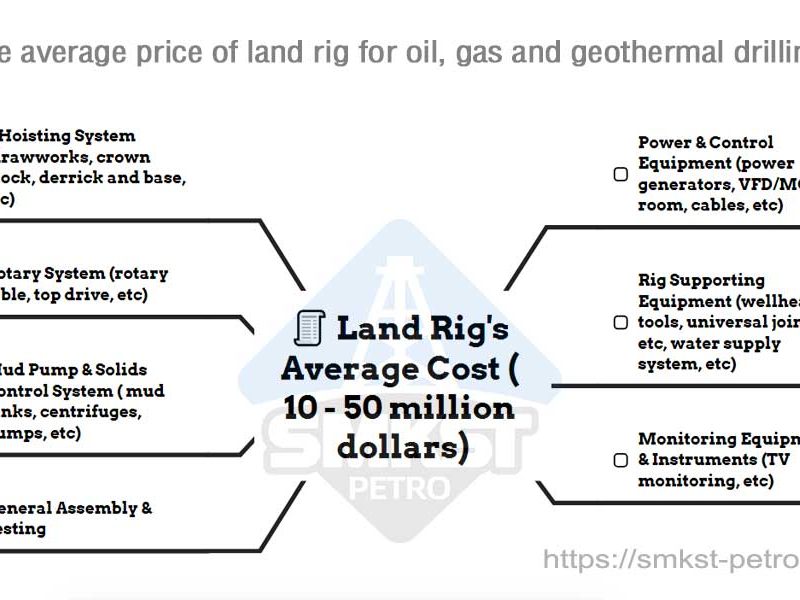
Published on: Jul 22, 2024
As global energy demand continues to grow and the exploration of onshore oil, gas, and geothermal reserves expands, the market for land rigs is experiencing significant growth. According to Westwood Insight’s latest World Land Drilling Rig Market Forecast released on December 7, 2023, global land rig demand will increase by 14% between 2023 and 2027. With this rising demand, we anticipate that rig prices will also experience some upward fluctuations. So, what is the current price of a land oil rig?
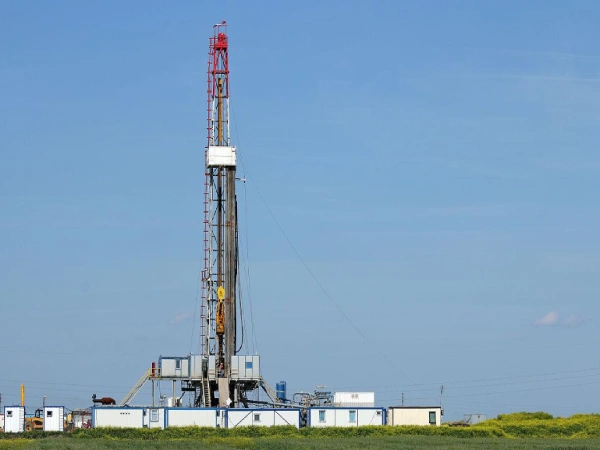
At SMKST, we specialize in the procurement, maintenance, and drilling services for land rigs designed for drilling depths exceeding one thousand meters. In this article, we will explore the pricing of land oil rigs and the key factors influencing their costs by incorporating recent oil acquisition news and examples of our client quotations.
How Much Does A Land Oil Rig Cost?
The cost of land oil rigs varies widely due to several factors. Less expensive rigs may cost $3 to $4 million, while high-end rigs can exceed $100 million. The average price range for oil rigs is between $10 million and $50 million. The specific price depends on the rig’s size, technological level, equipment configuration, and country of manufacture. Generally, the deeper the drilling depth, the higher the technological level and the more advanced the equipment configuration, making the rig more expensive.
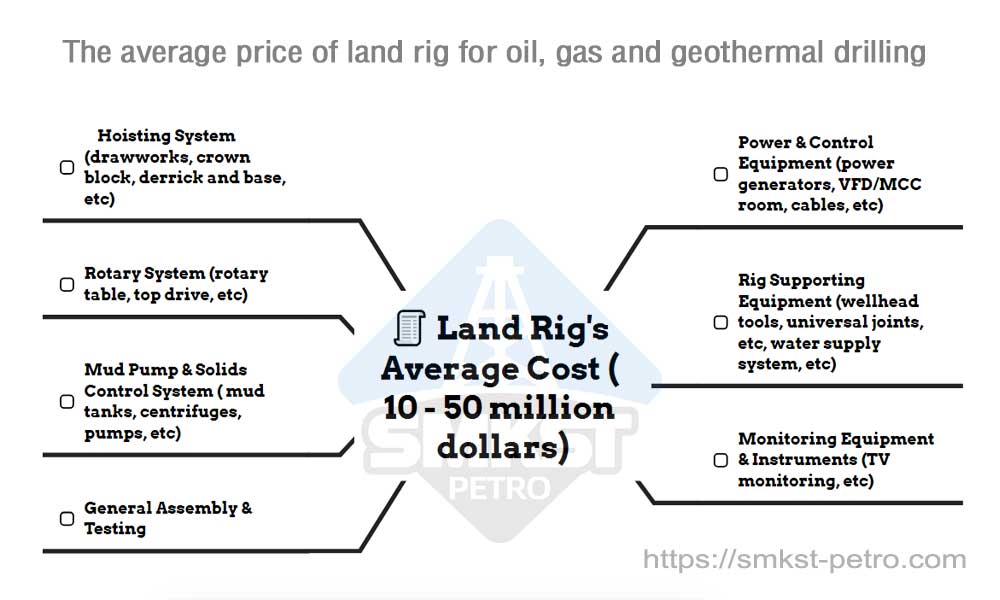
Factors influencing the cost of land rigs include equipment type and specifications, geographical factors, market demand, and supply chain conditions. For example, high-specification ultra-deep drilling rigs are more expensive than those designed for standard depths. Additionally, the costs will increase if the rig needs to operate in extreme environments, such as high-temperature deserts or frigid regions. Market demand fluctuations and supply chain stability are critical in determining costs. When market demand is high, and supply chains are tight, the price of drilling rigs may rise accordingly.
8 Major Factors Influencing Land Rig Price
What specific factors affect the cost of land oil rigs? Below, we delve into eight key factors that influence the cost of land rigs. These factors determine the initial construction expenses and significantly impact their long-term operation and maintenance.
1. Drilling Depth
Generally, the deeper the drilling, the more complex and costly the required equipment and technology. Deep well drilling demands more powerful equipment and higher maintenance costs. For instance, ultra-deep wells require more robust drill pipes and mud pumps for stability and efficiency. Advanced measurement and monitoring equipment are also necessary to ensure safety and accuracy. The geological and technical challenges of deep drilling need additional technical support and specialized equipment, all of which significantly increase the cost.
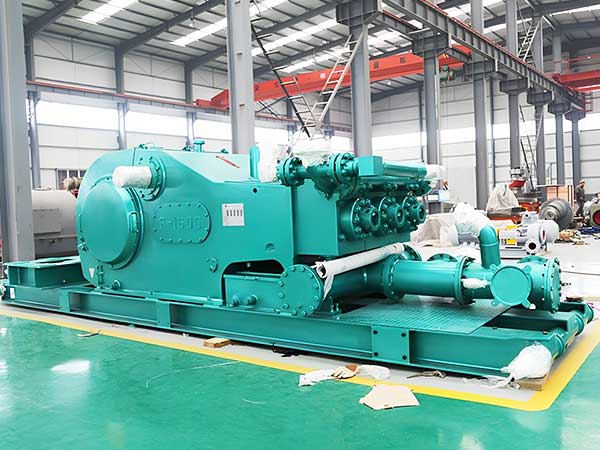
2. Geological Conditions
Different geological conditions significantly impact drilling operations. Complex rock layers, underground water, and fault zones require special drilling techniques and equipment, increasing costs. For example, drilling through hard rock needs high-strength drill bits and rods, and frequent bit replacements add to material and time costs. The presence of underground water may require additional measures to prevent intrusion and ensure drilling mud performance.
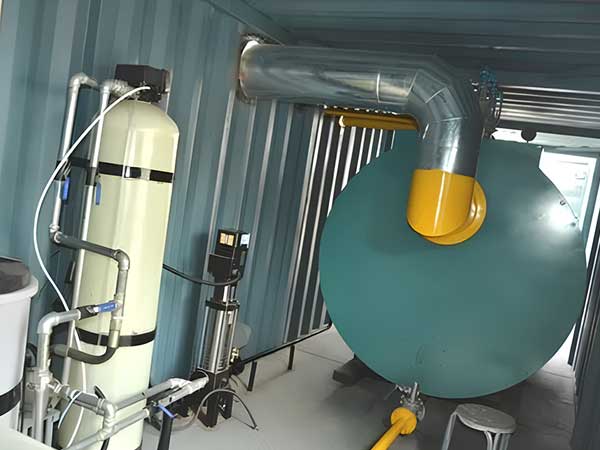
Complex geological conditions can increase wear and failure rates of downhole equipment, necessitating more maintenance and replacement costs. Directional drilling techniques may be needed to avoid unstable areas, adding complexity and cost.
3. Equipment Technology Level
Using the latest technology in your drilling rig, such as automation and remote control systems, can improve efficiency and increase initial investment. For example, Herrenknecht Vertical’s automated deep drilling rig, which requires only 20 people to operate, costs nearly $500 million.
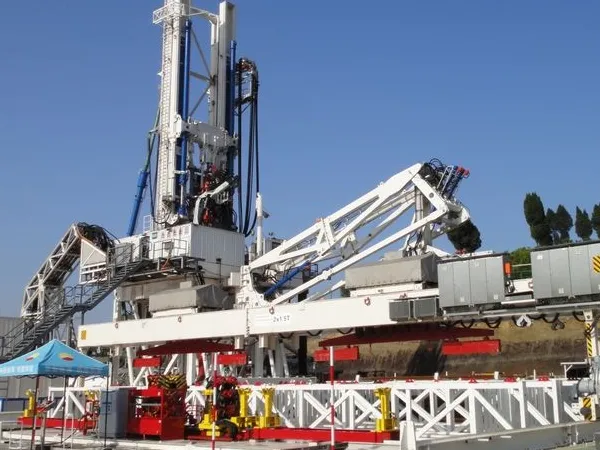
In contrast, traditional land rigs costing around three to four million dollars lack high-tech equipment and have lower initial costs. However, they also have lower drilling efficiency, requiring more operators and increasing the risk of human error and drilling accidents.
4. Supporting Infrastructure
The construction and maintenance of supporting infrastructure, such as camps, roads, and utilities, add to project costs. Drilling rigs are usually located in remote areas, requiring temporary camps to house operational and technical teams. Road construction and maintenance are essential, especially in complex terrain or harsh climates.
Water and electricity supply is crucial for regular operation, necessitating specialized facilities. These include long-distance pipelines, cables, temporary power stations, and water treatment plants. Environmental protection and resource management issues may further increase costs.
5. Labor Costs
Labor costs vary significantly by region and are a critical factor in manufacturing oil rigs. In countries like China, relatively low labor costs, combined with advantages in raw materials and other resources, enable Chinese oil rigs to maintain a similar technical standard to Western models while being 20-25% more affordable. This cost advantage spans manufacturing, R&D, assembly, testing, and logistics, enhancing the international competitiveness of Chinese rigs.

In contrast, labor costs are much higher in the United States and Europe, where higher wages, benefits, and work environment requirements increase manufacturing costs. Strict environmental and safety regulations add compliance costs, increasing the product price.
6. Environmental Protection Requirements
Stringent environmental protection requirements necessitate installing environmental equipment and additional measures, such as wastewater treatment and noise reduction devices. These measures minimize environmental impact but significantly increase project costs.
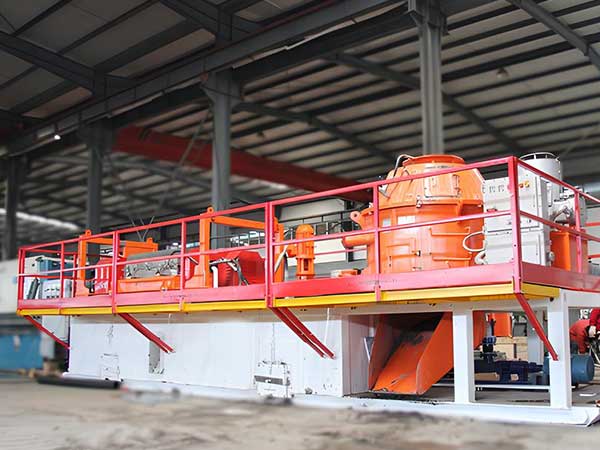
Advanced wastewater treatment systems prevent groundwater and environmental pollution, while noise reduction devices protect nearby communities. Environmental impact assessments and compliance with regulations require professional personnel, additional time, and funds, further increasing costs.
7. Suppliers and Brands
Brand influence is also important when choosing a rig. Equipment from well-known brands usually costs more due to the brand premium. However, big brands typically offer better warranties, after-sales service, higher production standards, and more reliable quality, providing peace of mind.
8. Additional Costs
Consider additional expenses such as transportation, installation, and long-term maintenance. Transportation costs will significantly increase for projects in high-latitude areas like the Arctic or Antarctic due to the higher technical requirements and costs of equipment.
Case Study: Cost Structure of a Land Rig
To understand the cost structure of a land rig, let’s take the example of a 2000HP land rig produced in China. This example outlines the main systems of a rig designed for drilling over a thousand meters deep and provides an approximate price range for each component.
If you need a more detailed quotation, please provide us with your specific drilling requirements, and we will offer you the most professional procurement service. Alternatively, you can browse our latest inventory of used oil drilling rigs, which includes photos, key specifications, and pricing.
2000HP Land Rig Major Components and Prices
No. | Component Name | Main Parts Included | Price (USD) |
1 | Hoisting Equipment & Accessories | JC-70B drawworks, hydraulic disc brake, DS70 eddy current brake, TC-450 crown block, JJ450/45-K3 mast, etc. | 882,000 |
2 | Rotary & Transmission Equipment | ZP375 rotary table, roller bushings, dual-purpose swivel, integrated chain box, etc. | 252,000 |
3 | Mud Pump & Solids Control System | F-1600 mud pump, mud pump filling system, pump drive assembly, drilling fluid manifold, solids control system, etc. | 791,000 |
4 | Power & Control Equipment | G12V190ZL1/O diesel engine coupler unit, driller’s control cabin, electric control system, air supply and purification unit, AC power supply system, auxiliary generator unit, etc. | 1,134,000 |
5 | Rig Supporting Equipment | General assembly parts, universal joints, on-site tools, oil supply system, water supply system, air system, mechanized wellhead tools, etc. | 196,000 |
6 | Monitoring Equipment & Instruments | Drilling instrument system, TV monitoring device, electronic digital anti-collision device | 77,000 |
7 | Oil & water tanks | Elevated oil tank, diesel tank, integrated water tank | 56,000 |
8 | General Assembly & Testing | General assembly and testing | 35,000 |
9 | Miscellaneous | Steel-wood foundation, inclinometer winch, welding machine, etc. | 77,000 |
Total Amount | 3,500,000 |
The land rig detailed above is widely used in China and can drill up to 7,000 meters (23,000 feet). The major components are from well-known Chinese brands, leading to price variations of up to $5000,000 depending on the brand.
Currently, many rigs are adopting top drive systems and intelligent drilling technology. These advanced rigs are generally more expensive and suitable for drilling operations in regions with high labor costs, such as developed countries or areas with high oil production. With the rise of artificial intelligence, oil rigs are gradually achieving full automation. AI applications in drilling include predictive maintenance, fault diagnosis, and optimization of drilling parameters, which reduce human errors and increase overall operational efficiency. Although these high-tech rigs can improve drilling efficiency and safety, the initial investment and subsequent maintenance costs can multiply.
For more information on recent large-scale procurement of oil rigs, here are some news links demonstrating the average prices in the tens of millions of dollars:
- Kuwait Oil Company clinches 63 rig contracts worth $670 million
- ADNOC orders ten hybrid rigs for $252 million
How to Choose the Right Land Oil Rig Based on Your Needs
Choosing a land oil rig is a complex decision-making process involving numerous factors. In addition to the significant factors influencing the cost of oil rigs discussed earlier, you should also consider the following points:
- Project Budget: The first step is to determine your project budget. This directly impacts the type and configuration of the rig you choose. High-performance rigs may have higher initial costs but could offer more significant economic benefits in the long run due to their efficiency and reliability.
- Supplier Delivery Time: Understanding the supplier’s delivery schedule is crucial to ensure the equipment arrives on time and avoids project delays. A reliable supplier should deliver the equipment on time and provide ongoing technical support and maintenance services.
- Commissioning Time: The time required to install and commission the equipment will affect the project timeline. Choosing equipment with shorter commissioning times and robust technical support can help you start production sooner, reducing waiting time and costs.
- Future Upgrade: As technology evolves and market demands change, your project might need upgrades. Therefore, the rig’s scalability and upgrade potential should be considered to meet long-term development needs.
By systematically evaluating these factors, you can make an informed decision to ensure project success. This approach optimizes your initial investment and provides security for future growth and profitability.
Conclusion
When calculating drilling costs, you should consider not only the cost of the land rig but also other expenses such as transportation and installation, daily operation and maintenance, technical upgrades, and personnel training. These additional costs will further impact the overall drilling cost.
As a professional company specializing in land drilling services for depths exceeding a thousand meters, SMKST can provide comprehensive support for procuring rig equipment and accessories in China. Our services cover all aspects of daily operations, including consumables and maintenance parts, ensuring smooth project execution. If you need to procure rigs and related accessories in China, don’t hesitate to get in touch with us.
Greetings!
I would the rig to be able to drill to a total depth of 75,000 feet to 100,000 feet!
We will require a minimum of 6,000 hp to 10,000 hp.