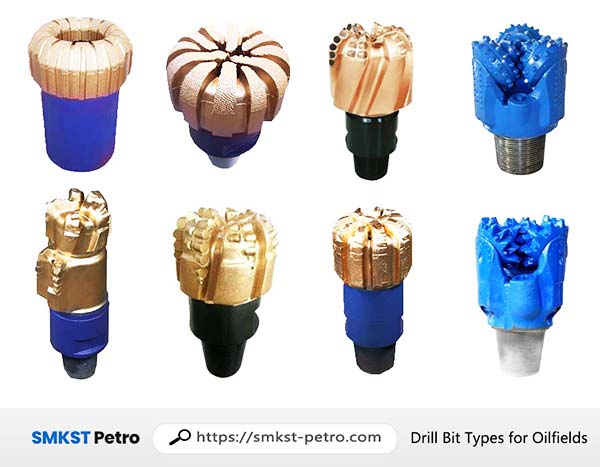
Published on: Oct 14, 2024
In oil, gas, and geothermal drilling, the drill bit is undoubtedly one of the core tools in the entire operation. It not only directly cuts through geological formations but also determines drilling efficiency, cost, and safety. Different geological conditions, drilling depths, and operational environments require different types of drill bits, making the selection of the right drill bit crucial.
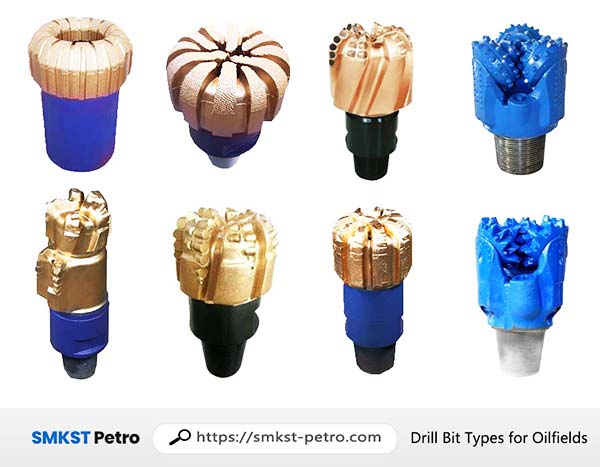
This article will introduce the common types of drill bits used in oil and gas drilling, their materials, classifications, and how to select the most suitable drill bit based on specific operational conditions. This will help you improve drilling efficiency and cost-effectiveness.
Part 1. Main Types of Drill Bits
There are various types of drill bits used in oil and gas drilling, but they can generally be divided into two main categories: roller cone bits and fixed cutter bits, depending on whether the cutting part rotates.
The roller cone bit mainly refers to cone bits, widely used in modern drilling. Fixed cutter bits, on the other hand, can be further divided based on the material and function of the cutting edges. Common types include drag bits, PDC bits, and natural diamond bits (mainly impregnated diamond bits). Additionally, drill bits can be classified based on their functions, such as coring bits, full-hole bits, reamers, and directional bits.
Let’s look at these types of bits and their application scenarios. (Note: Drag bits are no longer widely used and have been largely replaced by PDC bits, so we will not cover them in detail here.)
1. Roller Cone Bits
Since the first roller cone bit was invented in 1909, it has become widely used worldwide. The tricone bit is currently the most commonly used in rotary drilling operations. This bit type has various tooth designs and bearing types, allowing it to adapt to geological formations. By selecting the right tricone bit structure based on the formation being drilled, you can achieve satisfactory drilling speeds and bit penetration rates.
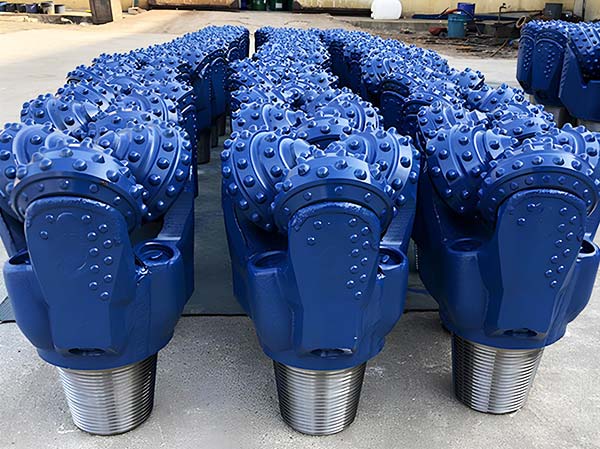
1.1 Tricone Bits Structure and Classification
A tricone bit consists of three cone-shaped rollers, with the bit body welded together and threaded at the top for connection. The rollers are made of metal with teeth, and the bit is categorized into two types based on tooth design: milled teeth (steel teeth) and insert teeth (tungsten carbide teeth). Milled teeth are suitable for soft to medium-hard formations and are more affordable, while insert teeth are made of extremely hard tungsten carbide, which makes them more expensive but suitable for harder, more complex formations.
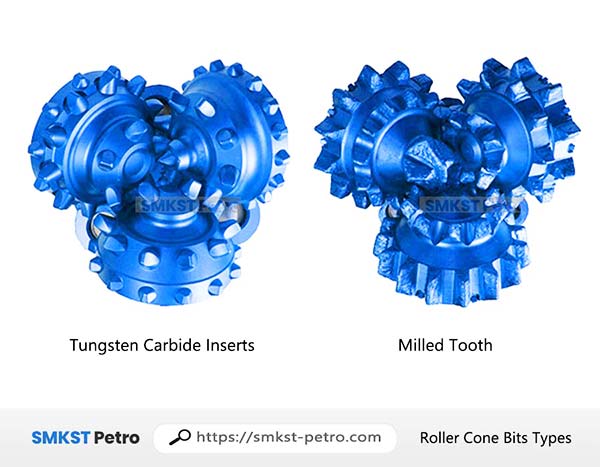
1.2 Roller Cone Bits Working Principle
When a roller cone bit operates at the bottom of the well, the bit rotates around its axis, known as “revolution,” while the three cones rotate around their own axes, known as “rotation.” The weight applied to the bit is transmitted through the teeth to the rock, crushing it. As the cones rotate, single and double teeth alternately contact the bottom of the well, causing the bit to vibrate vertically. This vertical vibration compresses and stretches the drill string, converting the elastic energy from these periodic changes into an impact force on the formation, aiding in rock fragmentation. This impact and crushing effect is the primary method by which roller cone bits break the rock.
In addition to crushing, roller cone bits also produce a shearing effect on the rock at the well bottom. As the cones roll, the teeth slide, scraping the bottom of the well in a manner similar to a drag bit. This sliding action is caused by the over-top placement, secondary cones, and off-axis arrangement of the cones. Generally, bits designed for soft to medium-hard formations feature all three design elements, while those for harder formations have just the first two. For extremely hard and abrasive formations, single-cone roller bits without over-top or off-axis features are commonly used.
2. PDC Bits (Polycrystalline Diamond Compact Bits)
PDC bits, short for polycrystalline diamond compact bits, are also known as synthetic diamond bits or composite cutter bits. Since General Electric introduced the first PDC bit in 1973, these bits have become widely used in oil drilling due to their high speed, long life, and high penetration rates. Almost all bit manufacturers have adopted this technology, producing their own series of PDC bits.
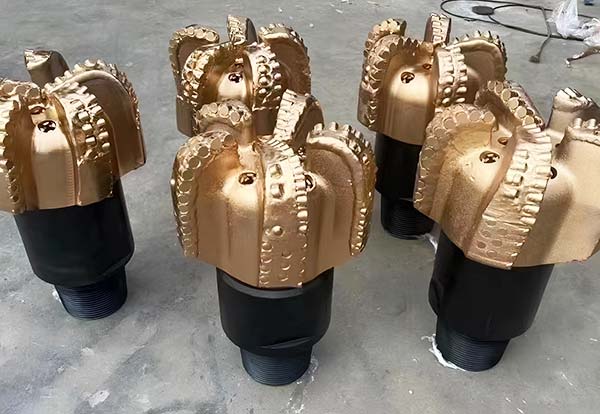
2.1 PDC Bits Structure
Based on manufacturing processes and structure, PDC bits can be divided into two types: steel-body PDC bits and matrix-body PDC bits.
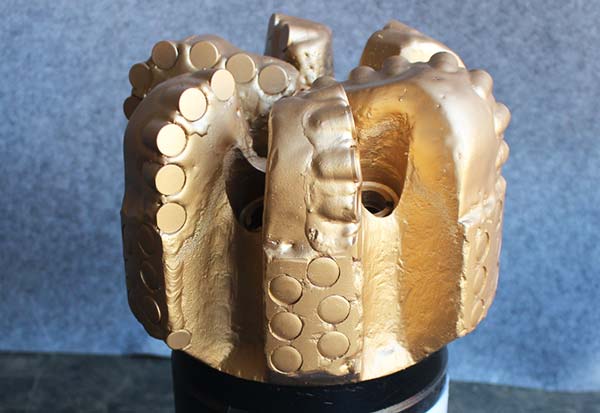
Steel body PDC bits are made from medium-carbon steel and manufactured through mechanical processes. PDC cutters are tightly pressed into pre-drilled holes in the bit body, with the crown surface hardened (e.g., with a tungsten carbide wear-resistant layer) to enhance durability. While these bits are simple to manufacture, their downside is the lower erosion resistance of the bit body, making it difficult to secure the cutters. As a result, they are less commonly used.
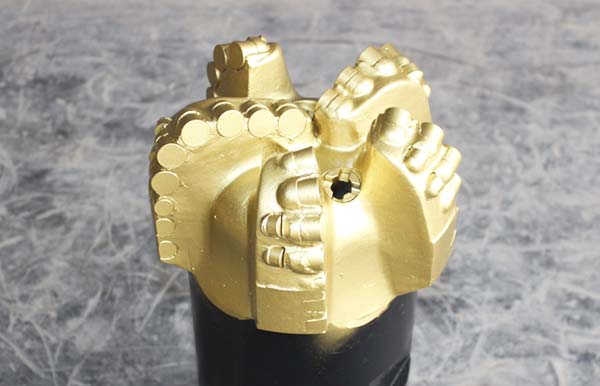
Matrix-body PDC bits feature a steel upper section and a wear-resistant tungsten carbide lower section, formed using powder metallurgy. PDC cutters are brazed into pre-formed slots in the matrix using low-temperature solder. The matrix’s high hardness and erosion resistance give these bits a longer life and higher penetration rates, making them more commonly used today.
2.2 PDC Bits Working Principle
PDC bits break rock through a cutting action. Under applied weight, the self-sharpening PDC cutters easily penetrate formations and shear the rock as they move forward under torque. Multiple PDC cutters work simultaneously, creating multiple free surfaces in the rock, which makes it easier to break. This results in high drilling efficiency and faster penetration rates.
2.3 How to Correctly Use PDC Bits
PDC bits are most effective in homogeneous soft to medium-hard formations. They are not suitable for gravel layers or formations with alternating soft and hard layers. For optimal performance, use low weight-on-bit, high rotation speed, and large flow rates. Before running a PDC bit into the hole, ensure the well bottom is clean and free of metal debris. When first running the bit into the hole, apply low weight and low rotation speed to establish the well bottom before resuming normal drilling. PDC bits have no moving parts, making them ideal for high-speed turbine drilling.
3. Natural Diamond Bits
Natural diamond is the hardest and most wear-resistant material known to humans, making diamond bits ideal for hard and abrasive formations, allowing for higher penetration rates. Despite being expensive, the longevity and penetration capabilities of diamond bits make them competitive in today’s oil drilling industry. Any drill bit that incorporates natural diamonds into its surface or matrix can be categorized as a natural diamond bit.
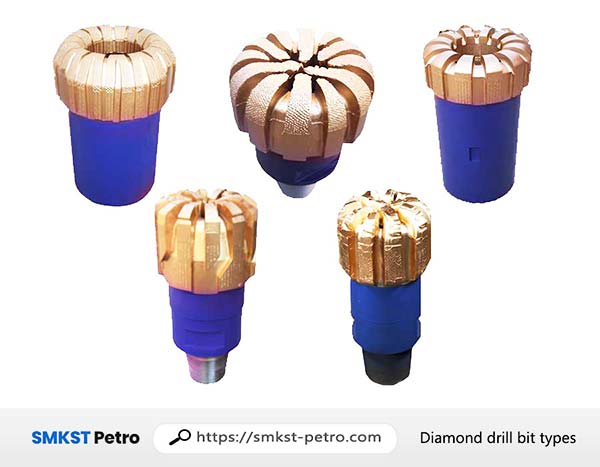
3.1 Diamond Bits Structure
Diamond bits are solid-body bits without any moving parts, mainly composed of the bit body, crown, hydraulic structure (including water ports, nozzles, channels, and debris grooves), gauge protection, and cutting edges (teeth). The crown is the working part of the bit, where natural diamond cutters are embedded to cut through rock formations. The hydraulic structure helps clear debris and cool the bit, while the gauge protection ensures the bit maintains the wellbore size. The bit body is made from either a tungsten carbide matrix or steel, and the upper part connects to the drill string through threads.
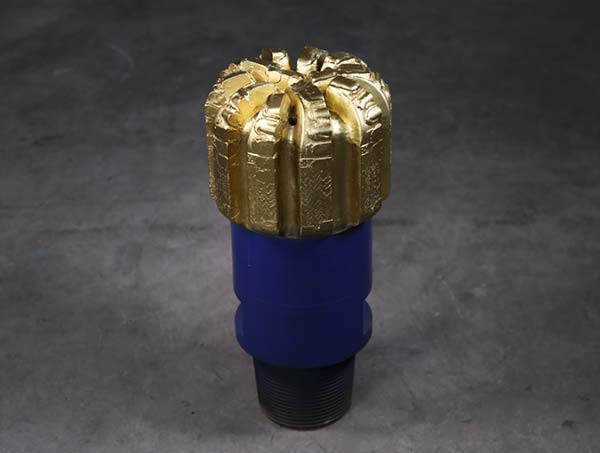
3.2 Diamond Bits Working Principle
When drilling, the multiple diamonds embedded in the bit’s surface act simultaneously on the rock. The way diamonds break rock varies with different rock types. In plastic formations, diamonds penetrate the formation under pressure, causing the rock ahead to fracture or deform plastically under torque, a process similar to plowing. This is known as plowing.
In brittle formations, the primary mechanism of diamond-bit rock destruction is crushing. Under pressure and torque, stress causes the rock beneath the cutting edges to fracture along the plane of maximum shear stress, leaving grooves behind the diamonds. The volume of rock fractured is much larger than the volume displaced by the diamonds, making this a volume-breaking process with high efficiency.
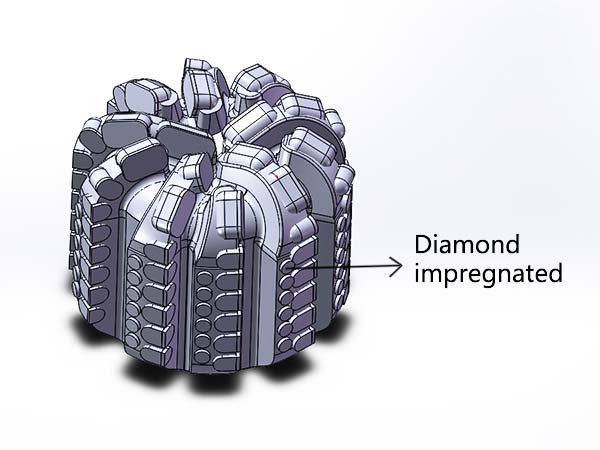
Impregnated diamond bits are typically used in hard formations like flint and siliceous dolomite. These bits feature fine diamond particles embedded in a matrix. As the bit grinds through rock, each exposed diamond particle acts as a small cutting edge, making the bit function like a tool with countless edges. This process is similar to grinding, which results in surface breaking with relatively low efficiency.
3.3 How to Properly Use Diamond Bits
Diamond bits are best suited for medium to hard abrasive formations, as well as for turbine drilling, deep wells, ultra-deep wells, and coring operations. Before using a diamond bit, the well bottom should be thoroughly cleaned to ensure no metal debris is present. When lowering the bit to the bottom of the well, use low weight and low rotation speed to avoid damaging the bit. Then, employ relatively low weight (compared to roller cone bits), higher rotation speeds, and large flow rates. Avoid excessive reaming whenever possible. If reaming is necessary, use low weight and low rotation speed to prevent damaging or over-wearing the gauge diamonds.
4. Hybrid Drill Bits
Hybrid drill bits are a relatively recent innovation in the drilling industry, developed to overcome the limitations of traditional bit types when operating in complex or interbedded formations. While the concept of integrating multiple cutting mechanisms has been explored for decades, the first commercially viable hybrid drill bit was introduced by Baker Hughes in 2011 with the launch of the Kymera™ hybrid drill bit.
A typical hybrid bit integrates multiple cutting elements, including diamond composites, roller cones, and PDC (polycrystalline diamond compact) cutters. Each component is selected for its specific strengths: roller cones provide superior impact resistance in hard or fractured formations; PDC cutters deliver high drilling speed and improved directional control in softer to medium formations; and diamond-enhanced materials increase durability and wear resistance, particularly in abrasive geological conditions.
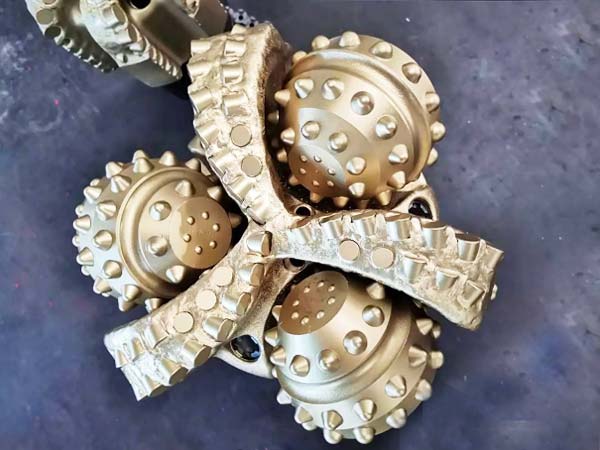
In one representative configuration, a 12 ¼ inch hybrid bit might utilize diamond-coated cutting structures alongside roller cones. The roller cones manage high-energy impacts from hard rock interfaces, while the PDC section—often equipped with optimized cooling channels—helps reduce bottom-hole torque and improves steerability, which is especially critical in directional and horizontal drilling. The hybrid approach distributes cutting forces across complementary mechanisms, allowing for smoother transitions across lithological boundaries. This design not only improves the rate of penetration (ROP) but also reduces vibration, extends bit life, and minimizes costly bit trips, making hybrid bits an effective solution for wells involving mixed formations or complex trajectories.
5. Other Bit Types
Aside from common roller cone and fixed cutter bits, there are many specialized bit types designed for specific operations, such as coring bits, full-hole bits, and bi-center bits.
5.1 Coring Bits
Coring bits are specifically designed to extract formation samples during drilling. Their unique design allows them to retrieve intact core samples, which are essential for oil and gas exploration. Geologists analyze these core samples to evaluate the lithology, porosity, and permeability of subsurface reservoirs, helping to determine the amount and recoverability of oil and gas. Coring bits are typically used during the exploration phase, especially in unknown or under-evaluated reservoirs. By using coring bits, drilling teams can obtain accurate geological data to support further development.
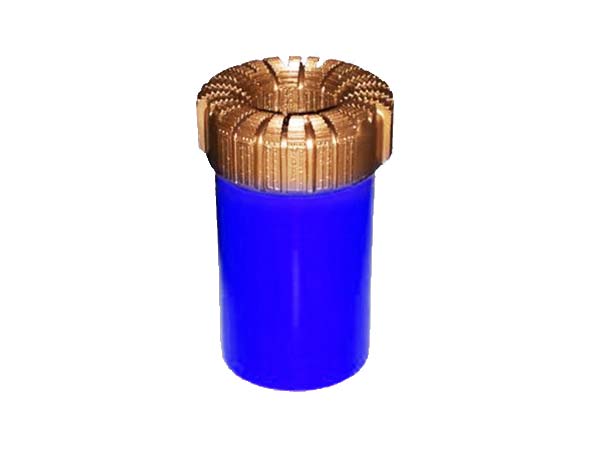
5.2 Full-Hole Bits
Full-hole bits are designed for drilling large-diameter wellbores. When larger well diameters are needed, full-hole bits can drill these in a single pass without requiring multiple reaming operations. These bits are often used in unconventional oil and gas wells, underground storage wells, and natural gas wells. Their main advantage lies in their ability to efficiently drill large-diameter holes, reducing the need for multiple-bit changes. For projects requiring large well diameters, full-hole bits are an ideal choice.
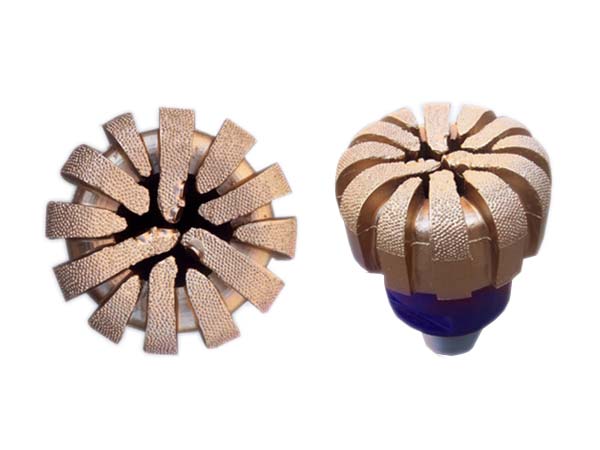
5.3 Bi-Center Bits
Bi-center bits are an innovative type of bit designed for hole enlargement during drilling. Their design allows them to expand the borehole diameter without increasing the initial hole size, reducing the need for traditional reaming tools. Bi-center bits are particularly suitable for formations that require transitions from smaller to larger diameters, making them ideal for projects that involve multiple hole diameter changes. By reducing the number of bit changes and reaming tool usage, bi-center bits improve operational efficiency and lower overall costs. They are especially effective in complex drilling operations requiring flexible wellbore designs.
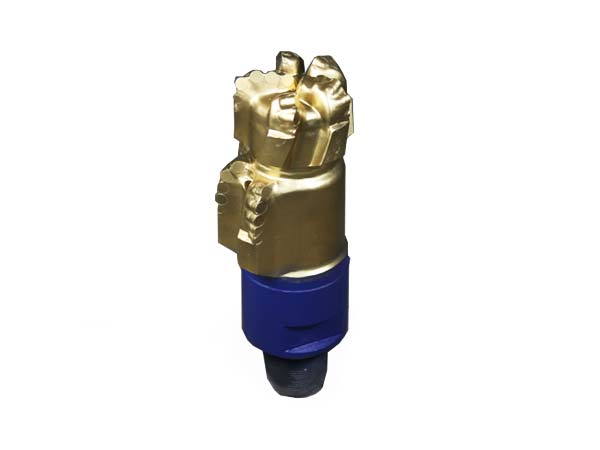
Part 2. How to Select the Right Drill Bit?
1. Selecting Roller Cone Bits
When selecting roller cone bits for oil drilling operations, it’s crucial to review the geological data and formation information from nearby wells. Combine this with the performance characteristics of the drilling equipment to choose the appropriate roller cone bit for the specific working conditions. The following principles should be emphasized during the selection process:
- Formation abrasiveness: Choose the roller cone bit model based on the abrasiveness of the geological formation and the hardness of the rock.
- Drilling techniques: Consider whether the operation involves curved or deviated drilling.
- Formation variability: Account for formations with alternating soft and hard layers.
- Depth of the well: The depth of the drilling operation also plays a key role in bit selection.
2. Selecting Diamond Bits
In modern oil drilling, PDC bits are widely used, especially in medium or soft formations. However, natural diamond bits are typically applied in complex geological environments with harder formations. A standard diamond bit consists of four components: the bit body, nozzles, matrix, and diamond particles. The main difference between a PDC bit and a traditional diamond bit lies in the fourth component, where PDC bits use synthetic polycrystalline diamond rather than natural diamonds. The advantage of diamond bits is their excellent cutting performance and adaptability to highly abrasive geological formations. They also have a distinct advantage in high-speed drilling.
3. Understand The IADC Codes
The International Association of Drilling Contractors (IADC) developed a global standard for the classification and numbering of drill bits. Understanding these codes can help you quickly identify a bit’s main characteristics, making the selection process easier.
3.1. IADC Tricone Bit Codes
1st Digit (Tooth Type) | 2nd Digit (Bearing/Seal Type) | 3rd Digit (Teeth Hardness) | 4th Digit (Additional Features) |
1-3: Steel Tooth (Soft to Hard Formations) | 1: Standard Open Bearing with Fluid Circulation | 1: Softest Teeth | A: Air Application |
4-8: TCI (Very Soft to Very Hard Formations) | 2: Standard Open Bearing for Air Drilling | 2: Medium Soft Teeth | R: Reinforced Welds |
3: Open Bearing with Gauge Protection Inserts | 3: Medium Hard Teeth | C: Center Jet | |
4: Sealed Ball & Roller Bearing with Fluid Circulation | 4: Hardest Teeth | S: Standard Steel Tooth | |
5: Sealed Ball & Roller Bearing with Gauge Protection Inserts | D: Deviation Control | ||
6: Journal Sealed Bearing | X: Chisel Insert | ||
7: Journal Sealed Bearing with Gauge Protection Inserts | E: Extended Jet | ||
Y: Conical Insert | |||
G: Extra Gauge Protection | |||
Z: Other Insert Shape | |||
J: Jet Deflection |
Tricone Bit Example:
- Code: IADC 517G
- 1st Digit: 5 (TCI, Soft to Medium-Hard Formation)
- 2nd Digit: 1 (Standard Open Bearing Roller Bit with Fluid Circulation)
- 3rd Digit: 7 (Hardest Teeth)
- 4th Digit: G (Extra Gauge Protection)
3.2 IADC PDC Bit Codes
1st Character (Body Material) | 2nd Character (Cutter Density) | 3rd Character (Cutter Size) | 4th Character (Profile) |
M: Matrix | 1: 30 or fewer 1/2 in. cutters | 1: Cutters larger than 1 in. | 1: Fishtail PDC Bit |
S: Steel | 2: 30 to 40 1/2 in. cutters | 2: Cutters from 9/16 in. to 1 in. | 2: Short bit profile |
3: 40 to 50 1/2 in. cutters | 3: Cutters of 1/2 in. | 3: Medium bit profile | |
4: 50 or more 1/2 in. cutters | 4: Cutters of 5/16 in. | 4: Long bit profile |
PDC Bit Example:
- Code: IADC M324
- 1st Character: M (Matrix body material)
- 2nd Character: 3 (40 to 50 ½ in. cutters)
- 3rd Character: 2 (Cutters from 9/16 in. to 1 in.)
- 4th Character: 4 (Long bit profile)
Conclusion
This article primarily covers the types of drill bits commonly used in oil and gas drilling. We also discussed how to select diamond bits and tricone bits. When drilling at depths exceeding 3,000 meters, the geological conditions can become more complex, often requiring multiple types of bits throughout the operation. By selecting the correct drill bit, you can greatly improve drilling efficiency, reduce operational costs, and ensure wellbore quality.
If you have drilling needs and are looking to buy high-quality, cost-effective drill bits in China, feel free to contact SMKST. With extensive experience in oil drilling and drilling accessories procurement, we can quickly provide various types of drill bits to meet your specific requirements.
This article Very interesting and fully covered all inquiries about drill bits type.