
Published on: Aug 28, 2024
Oil and gas drilling is a complex and costly operation that requires real-time downhole information to ensure safety and efficiency. In this process, LWD (Logging While Drilling) and MWD (Measurement While Drilling) technologies play crucial roles. MWD can be thought of as the “ears” of the drilling operation, capturing various physical data from the downhole tools, which is especially critical in directional drilling. On the other hand, LWD acts as the “eyes,” helping engineers understand the underground formations in real time. These two technologies work hand-in-hand to ensure precise and efficient drilling operations.
This article will delve into the basic principles of MWD and LWD technologies, their respective applications, and the main differences between them. This will help you better understand these technologies and their key roles in oil and gas drilling. Additionally, if you require directional drilling services, feel free to contact us. We offer global directional drilling services, particularly in Africa and the Middle East.
Part 1: What is MWD Technology?
MWD, or Measurement While Drilling, is a technology used to acquire real-time borehole trajectory and engineering parameters during drilling. MWD technology became widely adopted in the 1970s, initially used for monitoring and adjusting the borehole trajectory, especially in directional drilling. MWD technology primarily measures downhole engineering parameters such as inclination, azimuth, weight on bit, and torque in real-time, helping ensure that the drill bit follows the designed path and prevents the borehole from deviating from the target.

MWD tools are typically integrated into the bottom hole assembly (BHA), with data transmitted to the surface via mud pulse telemetry, electromagnetic waves, or wired drill pipe. This real-time data allows engineers to adjust drilling parameters as needed to maintain borehole stability and safety. MWD is especially critical in directional drilling, as it helps engineers accurately guide the drill bit to the target reservoir.
Part 2: What is LWD Technology?
LWD, or Logging While Drilling, is a method used to measure formation characteristics during drilling. LWD technology matured in the 1980s, designed to acquire real-time formation data using specialized tools during drilling. This data includes resistivity, gamma rays, density, porosity, and other critical parameters for evaluating the physical and chemical properties of the formation.
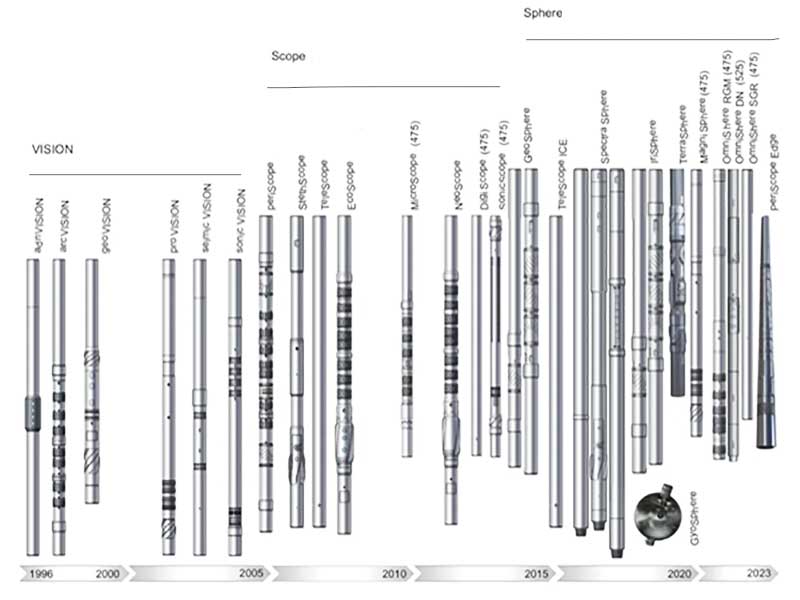
LWD tools are also installed in the bottom hole assembly and can transmit part or all of the measurements to the surface in real-time when integrated with the MWD system. This is known as “real-time data.” In some cases, the complete dataset from LWD tools is downloaded after the drilling tools are pulled out of the hole, known as “memory data.” The main advantage of LWD is that it can measure formation characteristics before drilling fluid invasion, providing critical formation information, especially in complex or high-angle boreholes where conventional wireline logging is not feasible.
Part 3: The Main Differences Between MWD and LWD
Although MWD and LWD are often used together in drilling operations, they have different technical focuses and application scenarios. To better understand the difference between MWD and LWD, we can compare them across several dimensions, such as primary purpose, measured parameters, and application scenarios.
Comparison Dimension | MWD (Measurement While Drilling) | LWD (Logging While Drilling) |
Maturity | 1970s | 1980s |
Primary Purpose | Real-time trajectory monitoring in directional drilling | Formation evaluation, optimizing reservoir development |
Measured Parameters | Inclination, azimuth, weight on bit, torque, etc. | Resistivity, gamma rays, density, porosity, etc. |
Application Scenarios | Ensuring accurate drilling direction, preventing deviation from target | Providing formation data, optimizing borehole position and reservoir output |
Data Transmission | Mud pulse telemetry, electromagnetic waves, wired drill pipe, etc. | Mud pulse telemetry, electromagnetic waves, wired drill pipe, etc. |
Data Processing | Real-time processing, supporting immediate decision-making during drilling | Combination of real-time and memory data, supporting detailed formation analysis |
Tool Integration | Integrated into bottom hole assembly, usually combined with directional drilling tools | Integrated into bottom hole assembly, working in conjunction with MWD systems |
Applicability | Suitable for directional drilling and borehole trajectory monitoring | Suitable for complex formation evaluation, especially in boreholes where wireline logging is not possible |
Part 4: Commonalities Between MWD and LWD
Despite their differences in specific functions, MWD and LWD share several commonalities that make them indispensable technologies in oil and gas drilling. First, both technologies are part of the while-drilling measurement system, capable of collecting data in real-time during drilling without stopping operations. This real-time capability allows engineers to obtain necessary downhole information at critical moments during drilling operations, enabling quick decision-making and avoiding potential risks. Together, these technologies improve drilling efficiency and safety, helping to optimize borehole trajectories and reservoir evaluations.
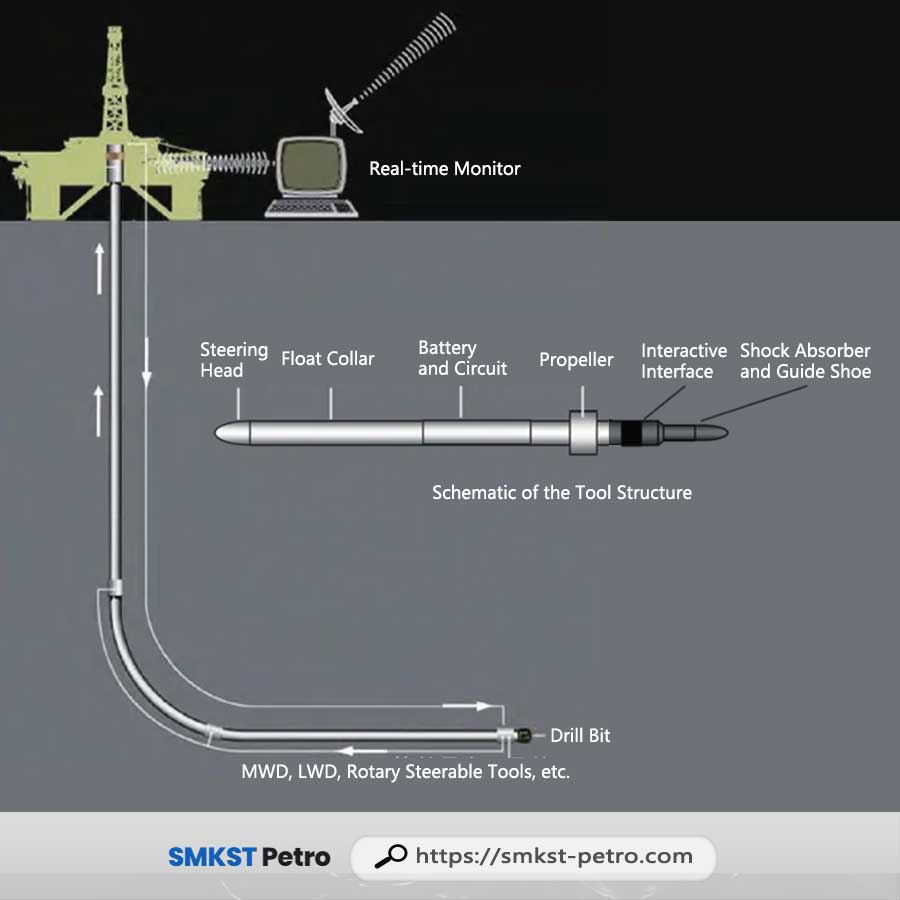
Moreover, both MWD and LWD technologies rely on similar data transmission methods, such as mud pulse telemetry, electromagnetic transmission, and wired drill pipe. These transmission methods ensure that downhole data can be transmitted to the surface in a timely manner for analysis and processing by surface operators.
Although their measurement focuses differ – MWD mainly on engineering parameters and LWD on formation characteristics – their synergy provides comprehensive downhole information. For example, combining MWD’s borehole trajectory data with LWD’s formation data allows engineers to adjust the drilling direction more accurately, ensuring the drill bit stays within the optimal geological target range.
Conclusion
The development of MWD and LWD technologies marks a significant milestone in the advancement of oil and gas drilling. From the initial simple measurement tools to today’s highly integrated intelligent systems, these technologies continue to enhance the safety and efficiency of drilling operations. MWD ensures the accuracy of the drilling path through real-time monitoring of drilling parameters, while LWD provides critical support for oil and gas exploration and development by measuring formation data in real-time.
In the future, as digitalization, automation, and intelligent technologies continue to progress, MWD and LWD technologies will keep evolving, offering more comprehensive and precise subsurface information for the oil and gas industry. The integration of technologies, faster data transmission rates, and intelligent applications will enable these “eyes” and “ears” to play an even greater role in oil and gas drilling.