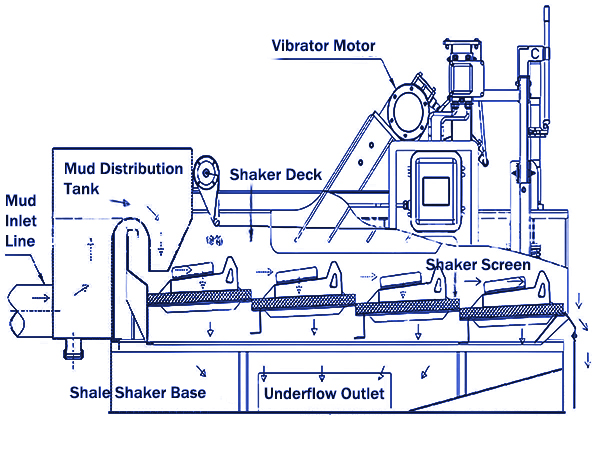
Published on: May 26, 2025
In today’s oil drilling operations, the shale shaker is the first and most critical part of the 5-stage drilling fluid purification. Its main job is to quickly and effectively remove drill cuttings from the returning mud. This helps protect downstream equipment, improves fluid recycling, and lowers drilling costs. But here’s the catch—there are many types of shale shakers out there. Each one performs differently in terms of capacity, clog resistance, and maintenance. A poor choice can easily drag down your whole system’s efficiency.
To help you make smarter shaker selections, the SMSKT engineering team created this practical guide. It starts with the basic working principle of a shale shaker, then breaks down 10 common types based on screen structure, vibration mode, frequency control, and smart features. Whether you’re handling high-flow mud, HPHT wells, or aiming for dry discharge, this guide will help you choose the right shaker for your operation.
1. Basic Structure & Working Principle of a Shale Shaker
Before comparing shaker types, it’s important to understand how a shale shaker works. A typical unit consists of three primary components: the base (hopper), the screen basket, and the vibrator motor unit. Drilling fluid enters the system through the mud inlet line and is directed into the inlet tank, where it is evenly distributed onto the shaker screens mounted within the screen basket.
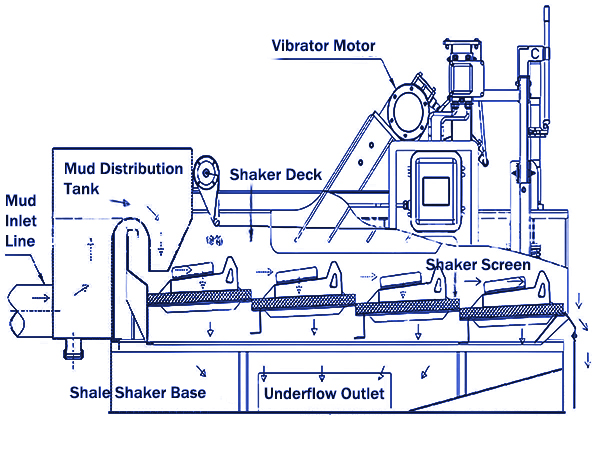
The vibrator motors generate high-frequency oscillations that drive the screen basket to move in a controlled pattern. These vibrations facilitate the separation process by conveying solid particles (such as drill cuttings) across the screen surface toward the discharge end. Meanwhile, the processed drilling fluid, also known as the underflow, passes through the screens and collects in the mud outlet located below the base. The separated cuttings exit the shaker along a designated cuttings discharge flow path.
The shaker’s separation efficiency and motion type—whether linear, elliptical, or circular—are determined by the shaker design and vibrator configuration.
2. 10 Different Types of Shale Shakers
Shale shakers can be categorized in several ways depending on their structural design, vibration characteristics, frequency range, and control systems—each affecting performance, adaptability, and maintenance needs in different drilling environments.
By Screen Deck Structure: Single vs. Double vs. Triple Deck
With the working principle in mind, the next key factor is the screen deck configuration, which directly affects separation performance and throughput. Based on the number and layout of screens, shale shakers are generally classified as single-deck, double-deck, or triple-deck models. Each configuration offers unique advantages in terms of efficiency, footprint, and adaptability to field conditions.
1) Single-Deck Shale Shaker
The single-deck shaker is the simplest design. It uses one screen layer and relies on linear or elliptical vibration to separate cuttings from drilling fluid. Known for its compact build, low cost, and easy maintenance, it’s ideal for basic jobs with low solids and smaller mud flow rates. Though it lacks the precision and speed of more advanced models, the single-deck shaker offers a budget-friendly, reliable solution for small to mid-sized rigs. Its ease of use and low upkeep make it a popular choice in operations where performance demands are modest.
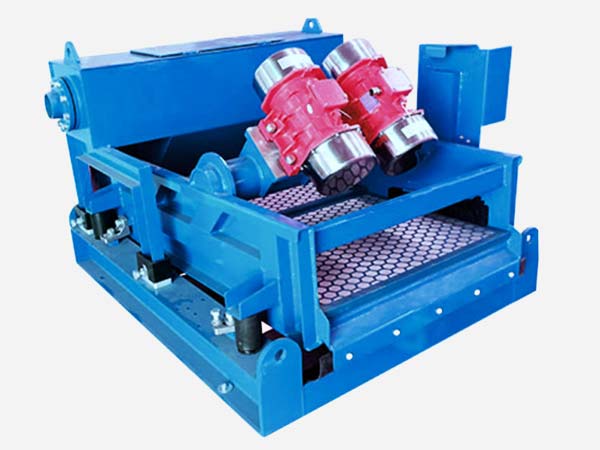
2) Double-Deck Shale Shaker
The double-deck shaker features two stacked screens that allow for layered separation. Mud passes through the top coarse screen first, which removes larger particles. It then flows to the finer lower screen for deeper separation. This design boosts separation accuracy and helps recover more usable fluid. It also increases processing volume and reduces strain on downstream equipment, extending the life of the entire solids control system. Double-deck shakers work best in wells with mixed particle sizes and medium to high flow rates. While they cost more upfront and require a bit more upkeep than single-deck units, the performance boost and durability make them a smart investment for more demanding jobs.

3) Triple-Deck Shale Shaker
The triple-deck shaker is a high-end option designed for demanding solid-liquid separation tasks. With three screen layers, it creates a multi-stage filtration path. As drilling fluid flows through each screen, solids are removed in steps, greatly improving separation precision and overall efficiency.
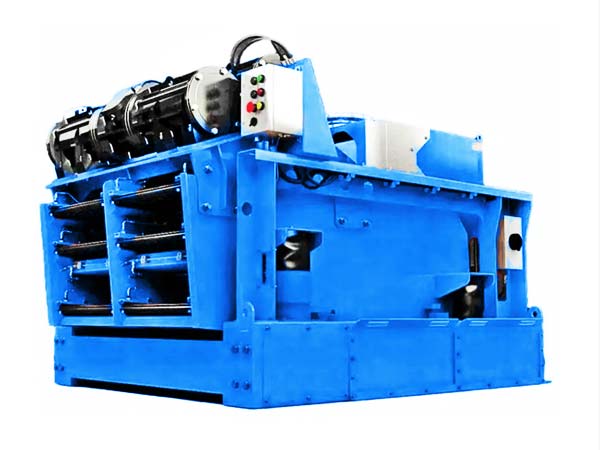
This type of shaker works especially well in challenging conditions like high-temperature, high-pressure wells, shale gas projects, or deep drilling operations where fluid quality is critical. Some models can even replace desanders or desilters, simplifying the entire solids control setup. Though it’s larger, heavier, and more expensive than double-deck models, its high throughput, minimal fluid loss, and dry discharge make it a must-have for advanced drilling projects.
Quick Comparison:
Category | Single-Deck | Double-Deck | Triple-Deck+ |
Decks | 1 | 2 | ≥3 |
Precision | Low | Medium | High |
Capacity | Low | Medium to High | High |
Footprint | Small | Medium | Large |
Cost | Low | Medium | Higher |
Best For | Standard drilling, budget-sensitive projects | Improved separation and fluid recovery | Deep wells, harsh or complex conditions |
By Vibration Mode: Linear vs. Elliptical vs. Balanced Elliptical vs. Dual Motion
The vibration mode of a shale shaker directly impacts how well it separates solids, how long the screen lasts, and how fast it drains the mud. Different motion patterns move solids across the screen in different ways. That’s why it’s important to consider the type of drilling fluid, the shape of solids, and your separation goals when picking a shaker.
4) Linear Motion Shale Shaker
Linear motion shakers are the most widely used type. They use two synchronized motors to create opposing forces, making solids move straight across the screen. This sharp, forward motion quickly pushes cuttings off the deck, boosting processing speed and capacity. They’re perfect for high-flow, high-sand drilling fluids and are often used in vertical or extended-reach wells. However, the intense vibration can wear out screens faster and cause blockages, so regular screen checks are a must. If your main goal is high throughput, a linear shaker is hard to beat.
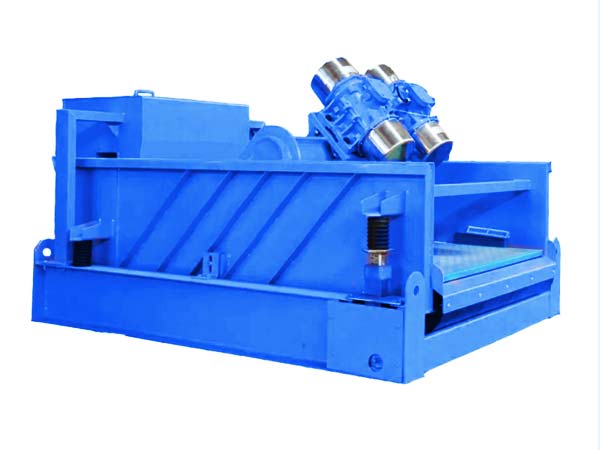
5) Elliptical Motion Shale Shaker
Elliptical motion shakers use two motors running slightly out of sync to produce an elliptical vibration pattern. This gentler motion keeps cuttings on the screen longer, improving separation accuracy and reducing the chance of clogs. They perform well with thick muds or fluids packed with fine solids, especially in shale formations. The softer vibration also extends screen life. While not as fast at removing solids as linear shakers, their steady and reliable performance makes them a solid choice for complex wells.
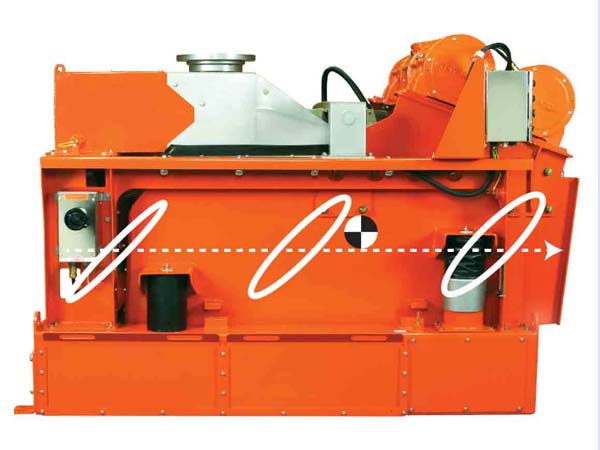
6) Balanced Elliptical Motion Shale Shaker
Balanced elliptical shakers take elliptical motion to the next level. With improved structure and dynamic balancing, they deliver smoother and more efficient vibrations. These models combine the speed of linear shakers with the clog resistance of elliptical ones. They run quieter, shake less, and handle fast-paced operations well, especially when drilling conditions change often. Though they cost more to build and maintain, their versatility and stable performance make them a top pick for high-spec drilling projects that demand both power and precision.
7) Dual-Motion Shale Shaker
The dual-motion shaker is a premium, multi-functional model. It can freely switch between linear and elliptical vibration modes. Some advanced versions even allow real-time control of the motion pattern through a smart system, adapting to different drilling phases or changing well conditions. This flexibility means it can handle everything from high-flow, low-solids fluids to thick, sticky, or mixed-particle mud. In high-intensity projects that require fast response to formation changes or continuous operation, the dual-motion shaker shines.
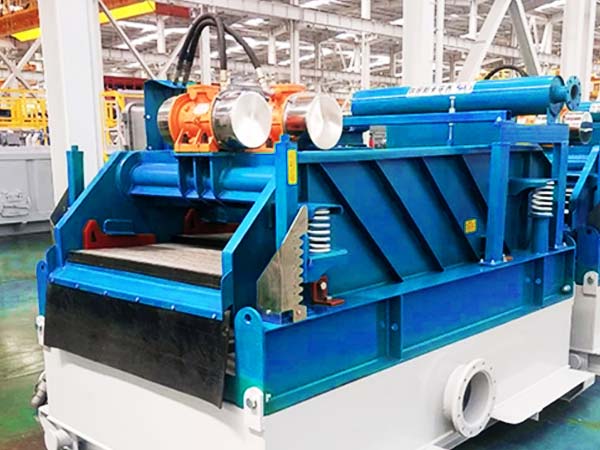
Yes, it comes with a higher price tag and requires skilled operation. But its ability to fine-tune performance on the fly makes it a top pick for deep wells, shale gas sites, and horizontal drilling operations where adaptability is key.
Shale Shaker Vibration Mode Comparison
Category | Linear Motion | Elliptical Motion | Balanced Elliptical Motion | Dual / Dynamic Motion |
Motion Pattern | Straight Line | Elliptical | Optimized Elliptical | Adjustable |
Discharge Speed | High | Medium | Medium-High | Variable |
Anti-Clogging | Low | Strong | Strong | Variable |
Cost | Low | Medium | Medium-High | High |
Best For | High-flow, easy muds | Sticky or complex muds | Projects needing speed + stability | Multi-phase, changing conditions |
By Frequency and Control System: Fixed vs. High-Frequency vs. Smart Control
Vibration frequency plays a key role in how well a shale shaker separates solids and handles fluid. Traditional models run at a fixed frequency, while newer, high-end shakers now offer variable speed and smart control systems. These upgrades help the equipment better adapt to different mud types and drilling stages, improving the overall efficiency of solids control.
8) Fixed Frequency Shaker
Fixed frequency shakers are the most classic design. They operate at a set frequency range and can’t adjust on the fly during drilling. This makes them simple, steady, and easy to operate. They’re commonly used in stable drilling environments where mud properties don’t change much.
With fewer electronics, they cost less to buy and maintain. That makes them ideal for low-budget operations or where flexibility isn’t a major concern. However, when well conditions change often or the mud makeup varies a lot, these shakers can struggle to keep up. Their separation performance tends to drop in more dynamic scenarios.
9) High-Frequency Shaker
High-frequency shakers boost the vibration speed and G-force to improve separation power. They’re designed to handle dense, sticky fluids packed with fine solids. These models shine when fast liquid recovery and low fluid loss are top priorities.
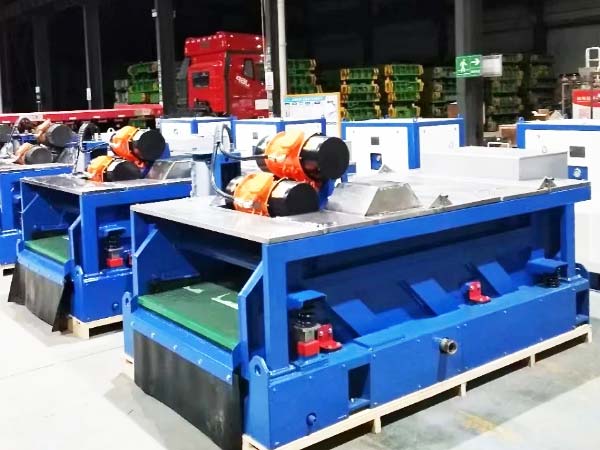
The strong vibration helps keep the screen clear and speeds up processing. But it can also wear out the screens faster and put more stress on the motor. That’s why they’re often used in high-demand jobs like shale gas drilling or ultra-deep wells. With high-frequency units, it’s important to balance performance with maintenance—shorter run cycles and regular checkups can help extend the machine’s lifespan.
10) Variable Frequency Shaker (VFD-Controlled Shaker)
The variable frequency shaker is one of the most advanced models on the market. It uses a Variable Frequency Drive (VFD) that allows operators to adjust both the vibration frequency and amplitude in real time. By doing so, they can fine-tune the G-force to match different drilling conditions without swapping out hardware. This flexibility is ideal for multi-stage wells, complex well paths, or any project where mud properties change frequently. With just a few adjustments, the shaker can shift modes to suit new conditions, boosting both efficiency and responsiveness on site.
Most VFD shakers also come with smart control systems. These offer remote monitoring, warning alerts, and energy management, helping extend screen life and keep operations stable. While the upfront cost is higher, the flexibility and performance gains have made variable frequency shakers the go-to choice for high-end drilling jobs.
Frequency Control Comparison
Category | Fixed Frequency | High-Frequency | Variable Frequency (VFD) |
Frequency Adjust | No | No | Yes |
G-Force Range | Fixed | High (>6 G) | Adjustable (3–8 G) |
Flexibility | Low | Medium | High |
Equipment Cost | Low | Medium | High |
Best For | Standard, low-budget wells | Dense or sticky mud drilling | Multi-stage, deep wells, shale gas |
3. Other Key Selection Factors & Maintenance Tips
Beyond deck structure, vibration mode, and frequency control, several finer details also impact a shale shaker’s real-world performance. These factors can influence everything from equipment lifespan to maintenance needs and overall project efficiency.
1) Screen Material & Structural Design
The shaker screen is both the most critical and most wear-prone part of any shale shaker. Thanks to advances in materials, composite screens are now widely favored over traditional steel- or plastic-framed ones. Made from layered stainless mesh and high-strength resin frames, these screens are lighter, more corrosion-resistant, and structurally stiffer, resulting in longer life and better performance.
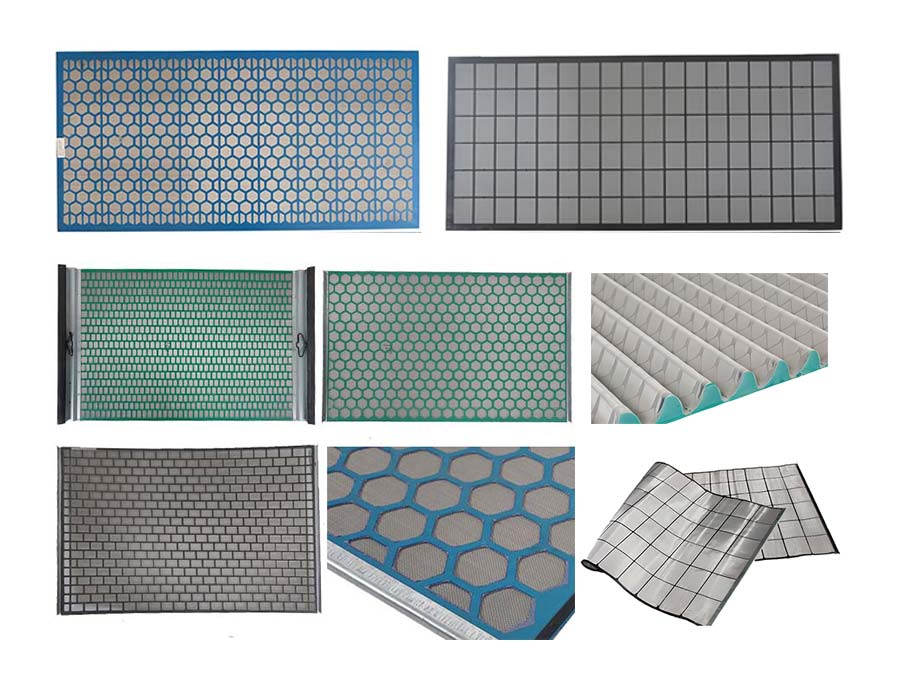
Don’t Miss: 5 Main Types of Shale Shaker Screens for Oil and Gas Drilling
3D screen designs like pyramid screens are also gaining popularity. Compared to flat screens, they offer over 25% more effective screening area. This makes them ideal for fast-flowing, high-volume operations. Choosing the right screen not only improves separation but also cuts down on screen replacements and reduces maintenance costs.
2) Vibration Force & Deck Angle Adjustment
The G-force, or vibration strength, is a key metric for evaluating separation power. Different drilling conditions require different G values—usually somewhere between 3 and 8 G. Higher Gs help throw off fluids quickly and improve dry discharge, but they also wear out screens and shaker parts faster.
To meet changing field conditions, many modern shakers now feature variable frequency drives that let you adjust vibration strength and amplitude in real time. Some units also include adjustable deck angle systems—either hydraulic or pneumatic. These let operators tweak the screen tilt based on mud thickness and flow rate, improving how long the fluid stays on the screen and enhancing overall separation. These small adjustments can make a big difference in both shaker efficiency and equipment lifespan.
3) Quick-Change Screens & Modular Maintenance Design
Smooth, efficient maintenance is key to keeping drilling operations running nonstop. On older shaker models, changing a screen often meant stopping the machine and needing multiple crew members—costly, time-consuming, and riskier.
To solve this, many modern shakers now feature fast-swap designs like snap-lock tensioning or quick-mount rails. These upgrades allow a single operator to safely replace a screen in minutes, without shutting everything down.
Modular design is another growing trend. Instead of dismantling the entire unit, operators can easily swap out screen frames, motors, or dampening systems. This reduces downtime and keeps productivity high, even during maintenance.
4) Smart Control & Remote Monitoring Systems
As automation becomes more common in drilling, smart controls are now a standard feature on high-end shale shakers. Many units come with PLC touchscreen interfaces, VFD control panels, and built-in alarm systems. These let operators monitor and adjust vibration frequency, amplitude, current, voltage, and more—all in real time. Some advanced models even connect to site-wide SCADA systems, allowing centralized control of multiple shakers, remote maintenance alerts, and real-time energy tracking.
These intelligent features not only boost safety but also give teams better insight into shaker health. They make it easier to fine-tune performance, catch problems early, and avoid issues like screen breakage or motor overload, greatly improving the system’s long-term reliability.
Conclusion
Choosing the right shale shaker is not just a technical detail—it’s a strategic decision that directly impacts drilling efficiency, fluid recovery, and overall project cost. As we’ve explored, factors like deck configuration, vibration mode, frequency control, and smart features each play a critical role in shaker performance.
Before making a selection, take a holistic view of your drilling conditions. Consider mud flow rate, solid content, fluid properties, and whether your operation spans multiple well sections or complex environments. The more accurately your shaker matches the job’s demands, the better your results will be in terms of throughput, reliability, and long-term cost savings.
At SMKST, we offer a full portfolio of high-performance shale shakers and shaker screens designed to meet these diverse needs, from single-deck units to double-deck and dual-motion systems with intelligent control. Contact us to find the best-fit solution and ensure your solids control system delivers maximum value at every stage of your operation.