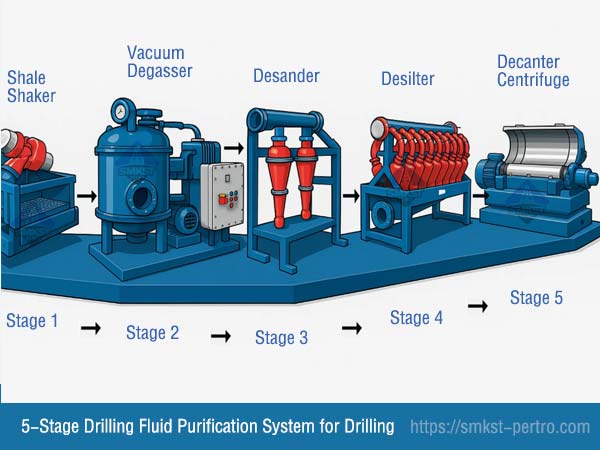
Published on: Mar 21, 2025
Is your drilling fluid clean enough to keep things running on your oil or gas drilling project?
Many drilling teams put most of their budget into the core rig package—drawworks, top drives, and mud pump units. However, the drilling fluid purification system is often overlooked. That’s risky. If solids in the mud are not properly removed, you can expect faster wear on pumps, shorter bit life, and more frequent fluid replacements. Costs go up. Efficiency drops. Downtime creeps in.
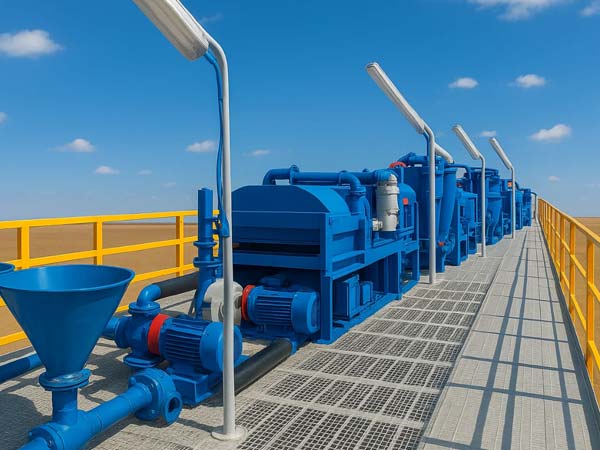
A solid 5-stage drilling fluid purification equipment for the mud circulation system can fix that. It keeps your fluid clean, your tools protected, and your job running smoother. In this article, SMKST walks you through every stage of the system—what it does, how it works, and why it matters.
Let’s break it down.
What Is a 5-Stage Drilling Fluid Purification in Drilling Rigs?
A 5-stage drilling fluid purification system is a group of solids control equipment designed to remove solids of different particle sizes from the drilling fluid. This system plays a vital role in oil, gas, shale, and geothermal drilling projects. Each stage targets a specific size range of solids, from large cuttings to ultrafine particles, keeping the mud clean, stable, and reusable. The goal? Minimize equipment wear, reduce mud loss, and improve drilling efficiency.
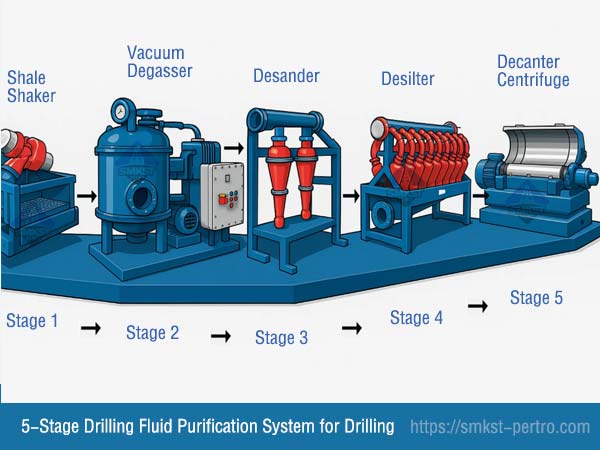
Here’s a quick breakdown of the five core components:
Stage | Equipment | Function |
Stage 1 | Shale Shaker | Removes large cuttings (>74μm) via high-frequency vibrating screens |
Stage 2 | Vacuum Degasser | Eliminates dissolved gases like methane and H₂S to prevent mud foaming |
Stage 3 | Desander | Removes medium-sized solids (45–74μm) using hydrocyclone technology |
Stage 4 | Desilter | Targets fine solids (15–45μm) with multiple smaller hydrocyclones |
Stage 5 | Decanter Centrifuge | Recovers barite and removes ultrafine solids smaller than 15μm |
How the Process Flows
The five stages follow the natural return flow of drilling mud—from the wellbore back to the surface. As the fluid carries drilled solids up, it first hits the shale shaker to remove the biggest chunks. Next, any trapped gases get pulled out by the vacuum degasser to stabilize the fluid. Then, the mud flows through the desander and desilter, which sort out medium to fine solids using cyclone force. Finally, the decanter centrifuge handles ultra-fine particles and helps recover valuable weighting materials, such as barite. Each stage does its part, so your mud stays clean, stable, and ready for reuse.
💡 Note
In some operations, a mud cleaner can serve as a combined alternative to Stage 3 and Stage 4 equipment, integrating both desander and desilter functions into a single compact unit.
Fluid Purification Equipment of Mud Circulation System
Each stage in the mud cleaning process plays a specific role in removing solids of different sizes. Let’s break down what each device does and how to make the right selection based on your drilling site needs.
Stage 1: Shale Shaker – The First Line of Defense
The shale shaker is where it all begins. This is the first—and often the most critical—step in removing solids from returning drilling fluid.
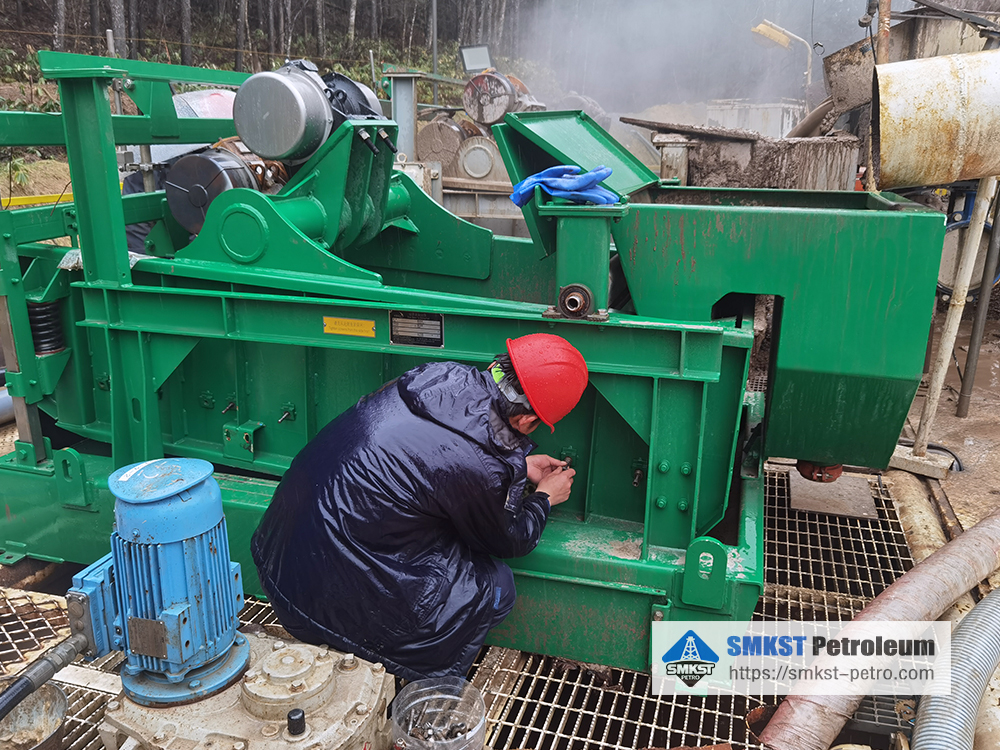
✅ How It Works
The shaker uses high-frequency vibration to separate large drill cuttings, typically those larger than 74 μm, from the fluid. The mud flows over a series of fine-mesh screens that allow liquid and small particles to pass through while holding back larger solids.
🛠 Common Screen Types
- Flat Screen: Lower cost, easier to replace
- Pyramid Screen: More surface area, higher throughput
- Hookstrip or Frame Type: Varies by shaker brand and model
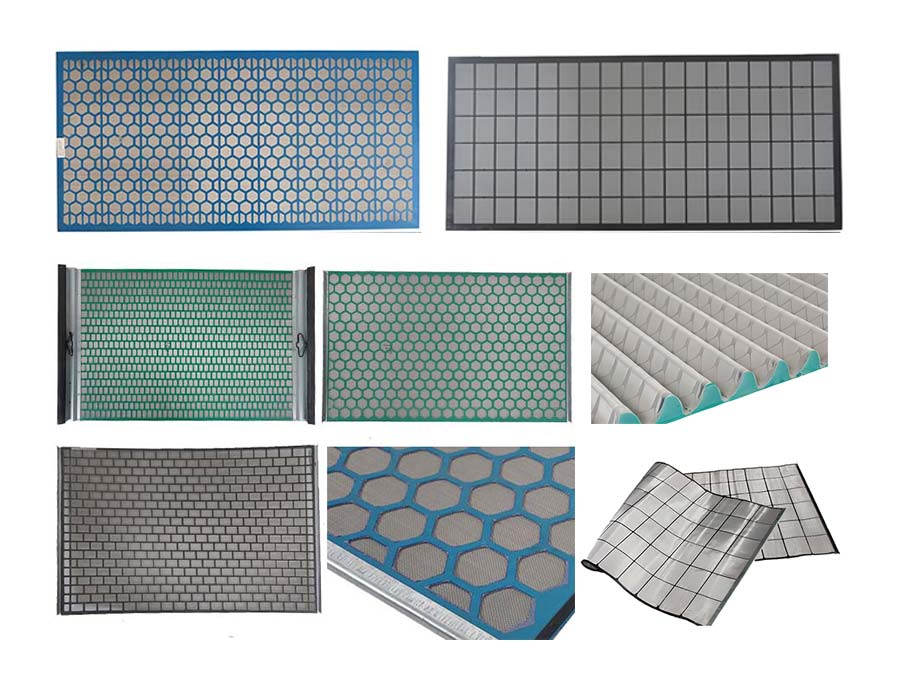
Choosing the right screen type and mesh size depends on the formation type, ROP (rate of penetration), and the overall solids loading in the mud.
💡 SMKST Tip
Not all shakers fit all rigs. Consider your drilling depth, expected cuttings volume, and mud viscosity when selecting a model. SMKST offers a range of shaker options, including standard, dual-deck, and high-G force models, to match different field requirements.
Stage 2: Vacuum Degasser – Stabilizing the Mud
Once the large solids are out, the next concern is gas. Dissolved gases, such as methane or hydrogen sulfide, can enter the drilling fluid, affecting its density and stability. That’s where the vacuum degasser steps in.
✅ What It Does
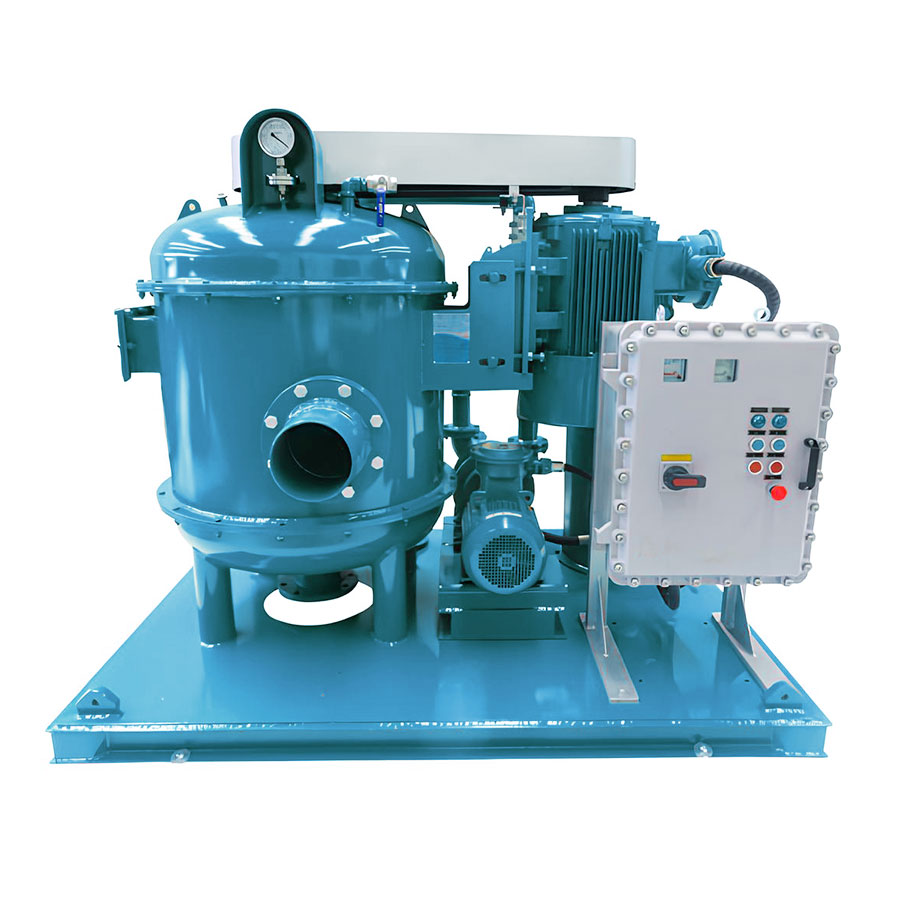
The degasser removes entrained gases by creating a vacuum chamber. Inside, the drilling fluid is sprayed or spread thinly, allowing trapped gases to escape. This helps prevent foam, maintain mud weight, and reduce the risk of blowouts or gas-cut mud.
🧪 When You Need It
- Gas-bearing formations
- High-temperature, high-pressure wells
- After lost circulation events
If your mud starts to foam or shows erratic weight readings, it’s likely that your system needs a degasser.
💡 SMKST Tip
Don’t wait until gas shows up in your pits. Plan degasser capacity based on well profile and expected gas content. SMKST provides vacuum degassers with various tank volumes and degassing rates—engineered for reliable performance in tough field conditions.
Stage 3: Desander – Removing the Mid-Sized Troublemakers
After gas removal, it’s time to deal with mid-sized solids that are too small for the shaker but still harmful to your mud system. That’s the job of the desander.
✅ How It Works
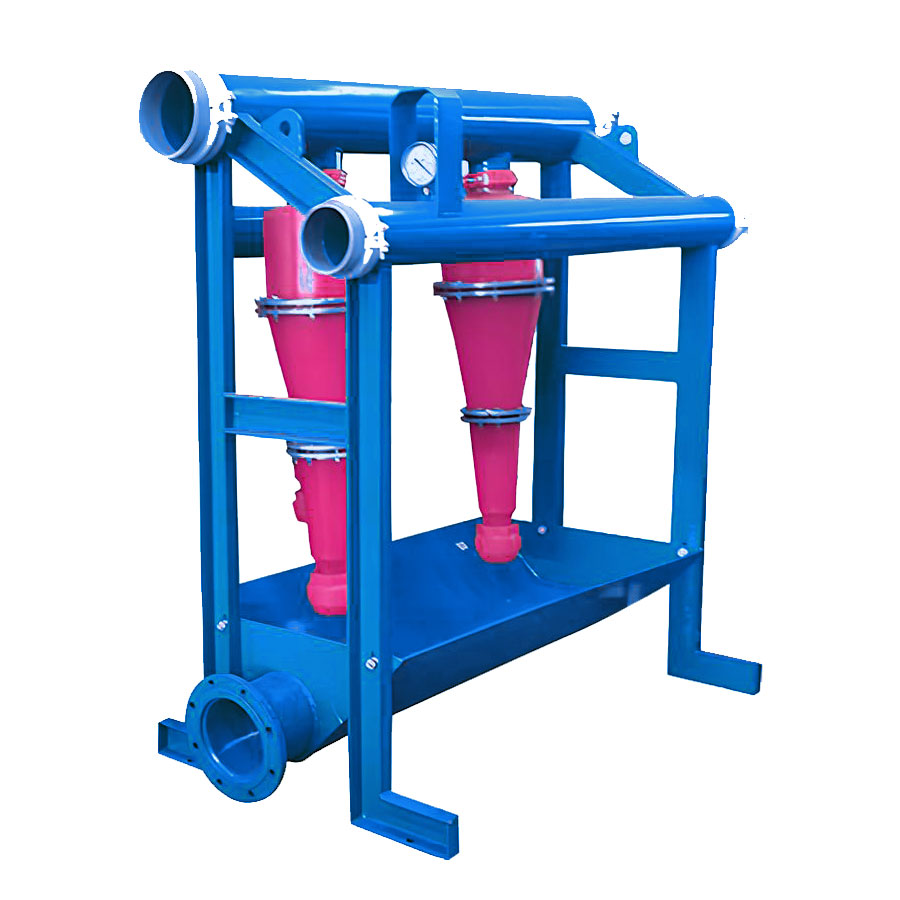
The desander uses hydrocyclones—cone-shaped devices that rapidly spin the drilling fluid. Thanks to centrifugal force, heavier solids between 45 and 74 μm are flung to the outer wall and drop out through the underflow. Clean fluid exits from the top. This stage protects downstream equipment, such as desilters and pumps, from excessive wear.
⚙️ Typical Setup
- Usually comes with 1–3 cones (10” diameter each)
- Flow capacity ranges from 500 to 1,500 GPM
- Often mounted on the same skid as the shaker for space-saving
💡 SMKST Tip
For best results, pair your desander with a fine-mesh underflow shaker. This lets you recover more usable mud and reduces waste. SMKST offers desander units with modular cone designs, making them easy to scale up or down based on your circulation volume.
Stage 4: Desilter – Precision for Fine Solids
Once mid-sized particles are out of the way, it’s time to tackle the finer stuff—those small but sneaky solids that can still cause big problems if left untreated. That’s where the desilter comes in.
✅ What It Does
The desilter is similar to the desander but uses smaller hydrocyclones—typically 4” cones—to separate particles between 15–45μm in size. (These fine solids might not be visible to the eye, but they can thicken the mud, mess with its rheology, and wear out precision tools like MWD sensors or rotary steerables.)

⚙️ Typical Setup
- Equipped with 8–20 cones, depending on flow rate
- Handles 50 to 1200 GPM
- Often mounted with its own underflow shaker (a.k.a. mini shaker) for drier discharge
💡 SMKST Tip
Desilters perform best when matched to the actual volume of mud being processed. Oversized units waste power, and undersized units miss solids. SMKST engineers help match cone count and size to your drilling fluid program for maximum efficiency and minimal fluid loss.
Stage 5: Decanter Centrifuge – The Final Barrier
Now we’re down to the smallest particles—those finer than 15μm. You can’t screen them. You can’t cyclone them out. But you still need to get rid of them to keep your mud system clean and balanced. That’s the job of the decanter centrifuge.
✅ What It Does
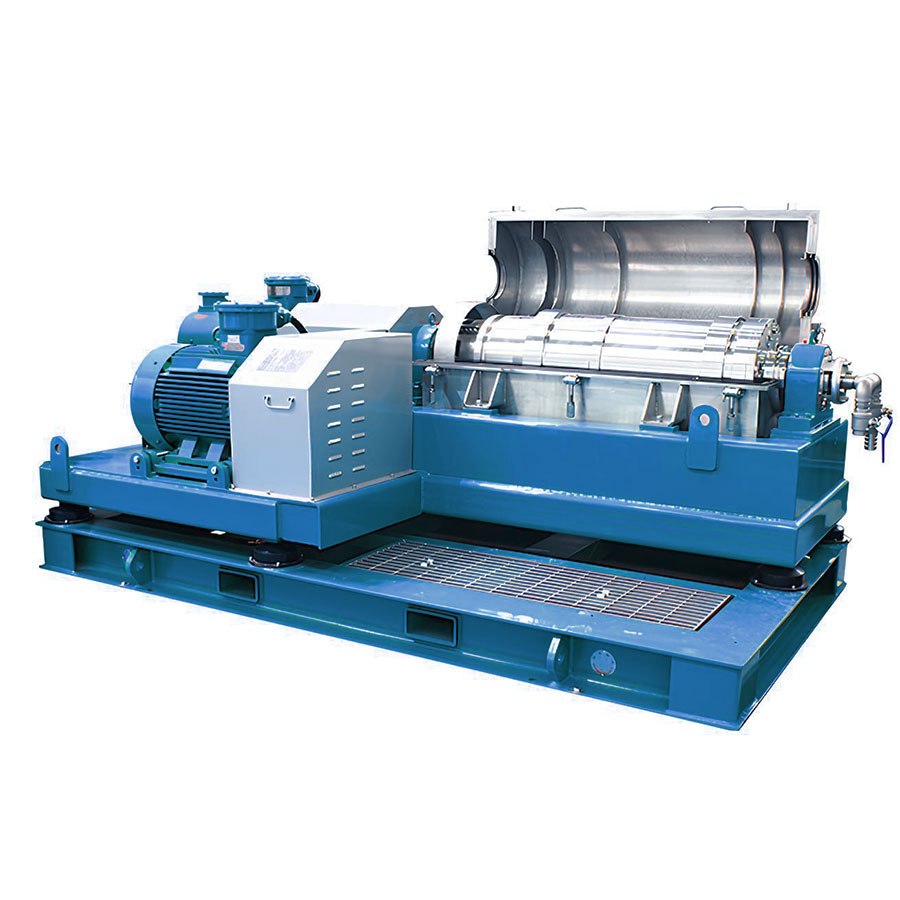
This machine spins drilling fluid at high speeds (often 1,800–3,200 RPM), creating intense centrifugal force that separates solids based on their density. The ultra-fine solids are pushed to the bowl wall and discharged, while clean fluid flows out through a weir or overflow.
It’s especially useful for:
- Controlling low-gravity solids
- Recovering barite
- Maintaining proper mud weight and viscosity
⚙️ Key Parameters
- G-force: Higher G means better separation
- Bowl speed: Impacts efficiency and capacity
- Feed rate: Must match your mud circulation rate
💡 SMKST Tip
Centrifuge settings aren’t one-size-fits-all. You need to balance G-force, bowl speed, and discharge solids content based on the drilling fluid type and solids load. SMKST offers both high-speed and variable-speed models, providing flexible performance on-site.
Mud Cleaner – Compact Combo for Desanding and Desilting
A mud cleaner combines desander and desilter hydrocyclones with a lower shaker deck in one integrated unit. It’s especially useful when rig space is limited or when higher solid-removal efficiency is needed in fewer steps.
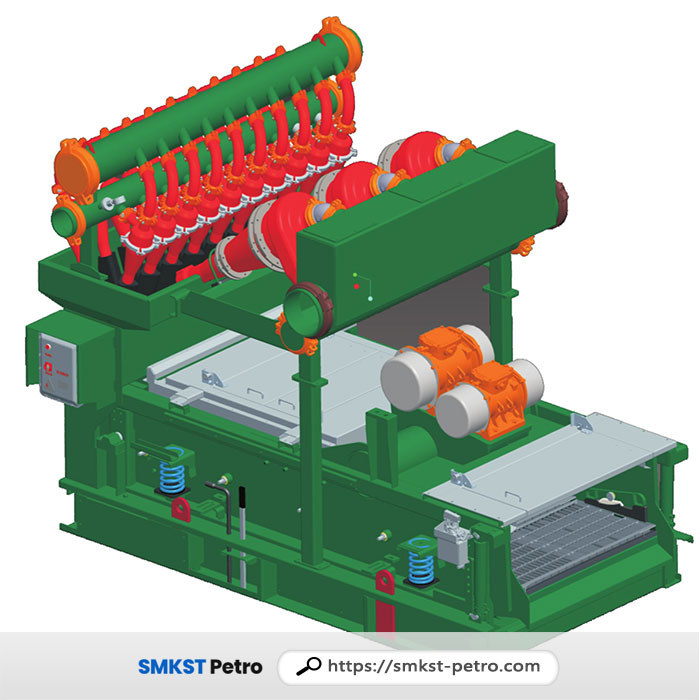
What It Does
The mud cleaner targets particles ranging from 15 to 74μm that escape the primary shaker. Hydrocyclones separate solids by centrifugal force, while the underflow solids are filtered again by the fine-mesh screen below—delivering cleaner fluid and lower waste volumes.
Other Modules That Support the 5-Stage Mud Cleaning System
While the five core stages handle most of the solids control work, auxiliary equipment ensures the system runs smoothly and meets specific fluid requirements. These modules may not always be required, but in many operations, they make a real difference.
1. Jet Mud Mixer
The Jet Mud Mixer is often used to blend additives like barite, bentonite, or polymers into the mud system. It uses a venturi hopper paired with a centrifugal pump to create a strong suction effect, ensuring fast and uniform mixing. This is especially useful when adjusting mud weight, viscosity, or filtration control during drilling.
2. Shear Pump
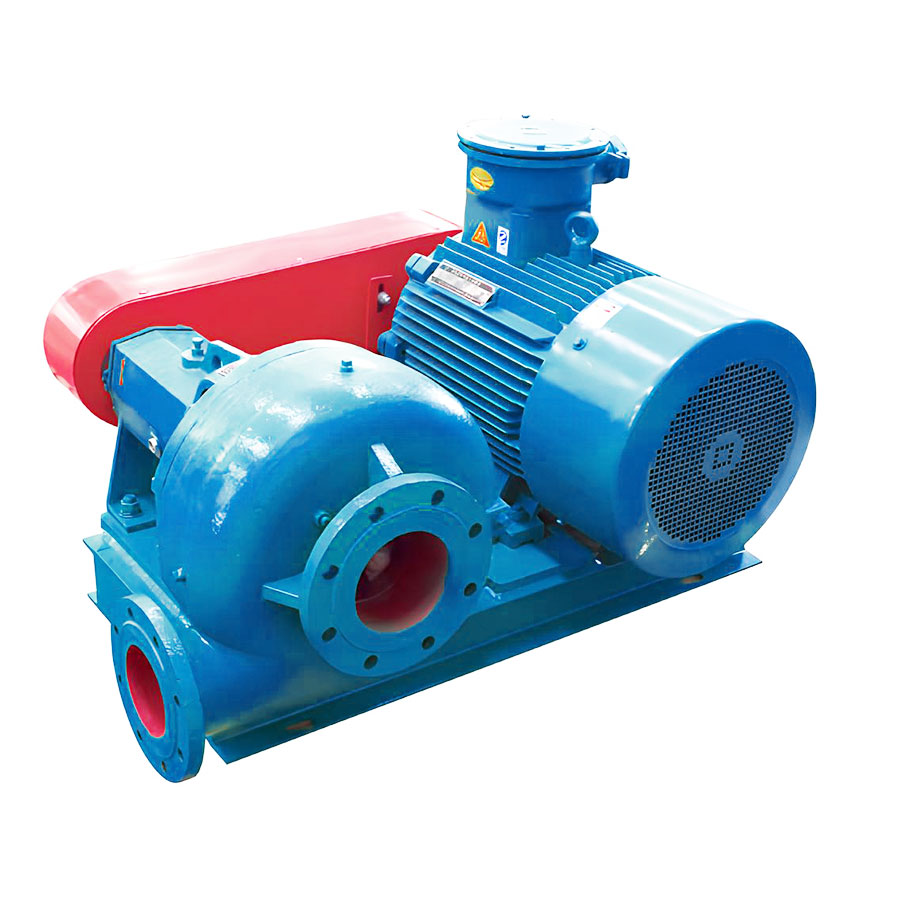
For wells using polymer-based fluids, a shear pump is a smart addition. It delivers high shear force to hydrate and disperse materials like PAC or CMC fully. This ensures better gel strength and prevents clumping, which can otherwise affect fluid stability and performance.
3. Mud Tanks and Agitators
The mud tank system, combined with mud agitators, helps maintain uniform mud properties throughout the operation. These tanks serve as intermediate storage between treatment stages. Agitators keep solids from settling and maintain proper suspension, especially during flow interruptions.
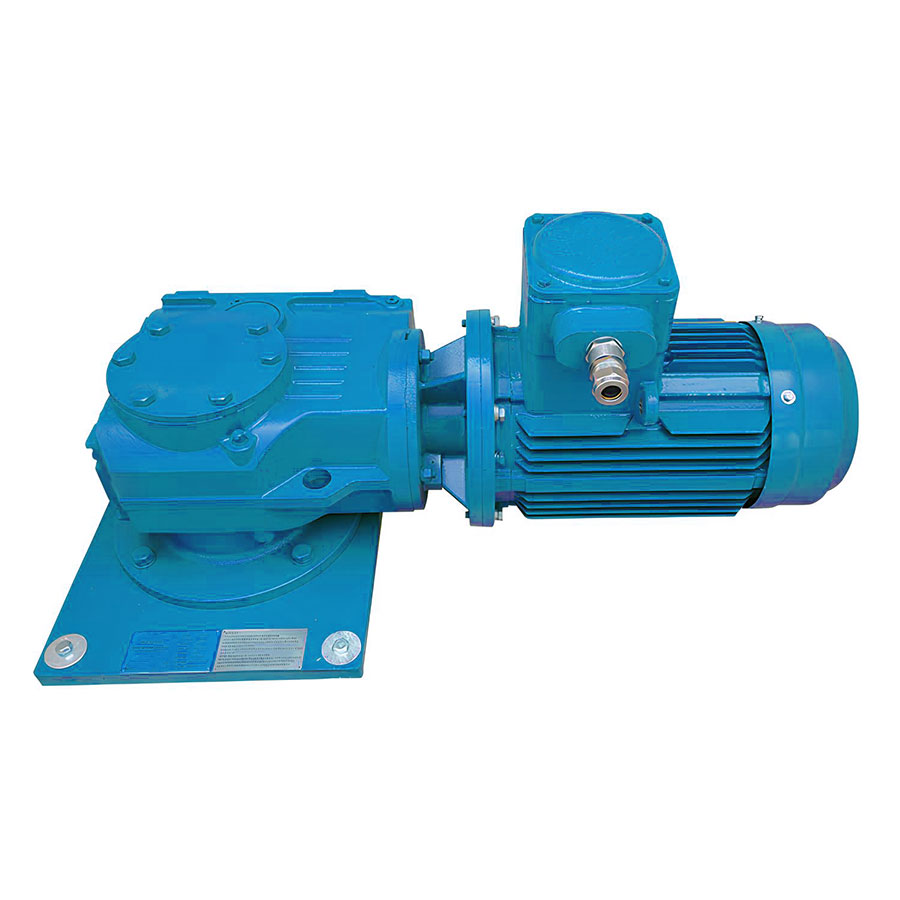
4. Screw Pumps or Sand Pumps
Finally, screw pumps and centrifugal sand pumps are used to transfer fluid between equipment stages. Screw pumps are better suited for handling high-density, abrasive fluids like barite-weighted mud, while sand pumps are ideal for general circulation tasks.
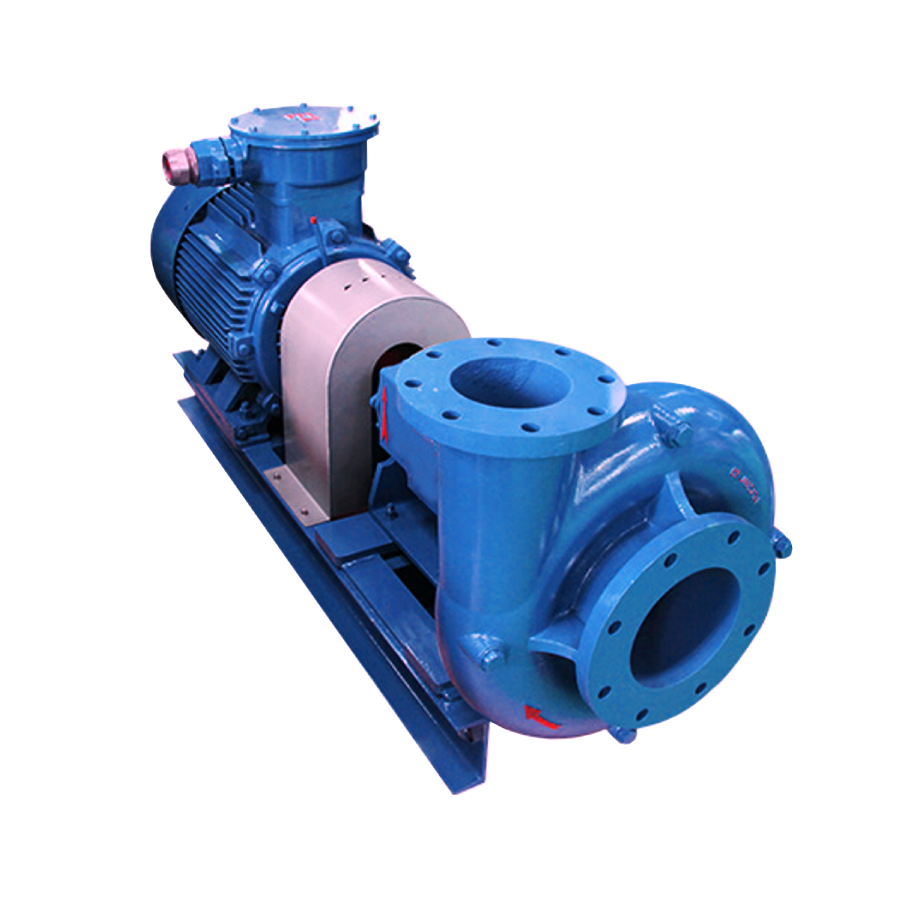
Conclusion
Each unit in the 5-stage purification system seems small compared to a rig or a mud pump. But together, they keep everything in balance. It reduces fluid losses, extends the life of your downhole tools, and helps you maintain drilling speed—all while lowering total operational costs.
At SMKST, we don’t just offer equipment—we deliver complete, field-proven solutions. From shale shakers to centrifuges, from tank systems to mixing units, we help you build a solids control package that fits your well profile, budget, and performance goals.
📞 Looking for a reliable solids control system for your drilling rigs?
Contact SMKST today to receive a customized proposal with full technical specifications, pricing, and expert on-site support.